Wednesday, April 29, 2009
Display problem ? Click HERE
Recommended :
- Tips on Succession in FREE Subscription
- Subscribes to FREE Hydrocarbon Processing
Sound Power Level (PWL) is the acoustic energy generated by a pressure reduction device. There are several ways to assess the adequacy of the piping to resist AIV fatigue. One of the way to ensure piping downstream of pressure reducing device sufficiently strong to resist AIV fatigue is to ensure the PWL allowable limit of downstream piping higher than the PWL generated by the pressure reducing device. Refer to "Sound Power Level (PWL) Prediction" for equation in prediction PWL.
A piping will have it stiffness and resistivity against vibration. It is very much subject to piping diameter, material properties, wall thickness, distribution of masses, pipe support, etc. Allowable sound power level and/or dynamic stress of piping can be a measurement of this resistivity of piping against excitation due to AIV. Several allowable PWL curves for piping which derived from different method i.e. "D-method", "D/t-method ", "E-method", etc have been used. Besides PWL related method, there are other method i.e. "Dynamic stress method", "Likelihood of Failure (LOF) method", etc which adopting allowable stress level also been used.
"D/t-Method"
Based on data available in Carucci & Mueller (1982) studies, "No failure" and "Failure" points have been plotted in following chart with Sound Power Level (PWL) versus Pipe Diameter / Wall thickness (D/t).
Note :
1) A "failure" point (0.3m, 165dB) is below curve. It is failed on bad welding. No further failure after good welding.
2) Red point are "failure" point and Blue point are "No failure" point
3) May be used for 0.2m < D < 0.9m. Use at risk for D < 0.2m and D > 0.9m
PWL Limit Equation For "D/t-method"
Eisinger (1997) has proposed a PWL limit line (blue line).
PWLlimit = 176.6 - 125 (D/t)
In this post, a new PWL limt line has been derived and following equation representing this line (black line).
PWLlimit = 203 - 8.4 Ln (1000D/t)
where
PWLlimit = Maximum allowable PWL at Pipe diameter D meter, (dB)
D = Pipe diameter, (m)
t = Wall thickness, (mm)
This line may be used to assess potential failure of piping downstream of pressure reducing device. Any point above the line potentially fail on AIV, piping treatment or redesign required to minimise the risk of AIV failure. This will be discussed in future...
There is additional discussion on unclear area and now proposed polynomial PWL limit line. Read more in "Assess AIV with "D/t-method" with Polynomial PWL Limit Line".
Related Topic
- Extra Attention to Common Point and Similarity on AIV Failure
- Piping Excitation When Expose to Acoustic Energy
- Acoustic Induced Vibration (AIV) Fatigue
- Sound Power Level (PWL) Prediction from AIV Aspect
- Several Criteria and Constraints for Flare Network - Piping
- Flow Element (FE) Upstream or Downstream of Control Valve (CV) ?
Sunday, April 26, 2009
Display problem ? Click HERE
Recommended :
- Subscribe FREE - World Pumpv (USA & Europe only)
- Tips on Succession in FREE Subscription
In today’s complex and frequently rugged process plant environments, liquid pumps are often over-worked and under-protected from adverse operating conditions. Many pumps run nearly non-stop 24-hours a day over multiple shifts. Poor operating conditions can reduce pump performance, require extra maintenance, shorten their lives and increase costs.
- Subscribe FREE - World Pumpv (USA & Europe only)
- Tips on Succession in FREE Subscription
Unexpectedly losing a pump is often an expensive or even a dangerous problem in a chemical plant. The results of a pump failure potentially range from the loss of product in sensitive pharmaceutical batch control applications to damage to other nearby equipment from pressure build-up of material that isn’t moving or even to safety hazards when a pump fails to shut-down and literally burns-up in the presence of combustible materials. It really pays to protect and care properly for your pumps. Read more here
DownloadRelated Post
- Basis & Tips on Setting Centrifugal Pump "Warming" Recycle Flow
- Removal of Specific Heat ratio (k) in the Mach No. & Critical Pressure Calculation
- Two Useful Equations For Flow Conversion between Air - Vapor & Actual - Standard
- Potential Problem associate with Double NRV in Series within a Line
- Restrcition Orifice Used in Many Applications in Different Manners
- A refresh to Process Engineer on few phenomenons in restriction orifice
- Why Restriction Orifice is some distance from Blowdown valve ?
Labels: Pump
Friday, April 24, 2009
Display problem ? Click HERE
Recommended :
- Tips on Succession in FREE Subscription
- Subscribes to FREE Hydrocarbon Processing
High frequency acoustic excitation downstream of pressure reducing device and potential of downstream piping failure on Acoustic Induced Vibration (AIV) has raised concern in many plant design. Earlier post "Extra Attention to Common Point and Similarity on AIV Failure" has discussed the common points and similarity of AIV such as typical failure location, system experienced failure in the past, failure time & period and Mach no. An engineer assessing AIV shall pay extra attention in these factors.
Sound Power Level (PWL) is the acoustic energy generated by a pressure reduction device. There are several ways to assess the adequacy of the piping to resist AIV fatigue. One of the way to ensure piping downstream of pressure reducing device sufficiently strong to resist AIV fatigue is to ensure the PWL allowable limit of downstream piping higher than the PWL generated by the pressure reducing device. Refer to "Sound Power Level (PWL) Prediction" for equation in prediction PWL.
A piping will have it stiffness and resistivity against vibration. It is very much subject to piping diameter, material properties, wall thickness, distribution of masses, pipe support, etc. Allowable sound power level and/or dynamic stress of piping can be a measurement of this resistivity of piping against excitation due to AIV. Several allowable PWL curves for piping which derived from different method i.e. "D-method", "D/t-method ", "E-method", etc have been used. Besides PWL related method, there are other method i.e. "Dynamic stress method", "Likelihood of Failure (LOF) method", etc which adopting allowable stress level also been used.
"D-Method"
Based on data available in Carucci & Mueller (1982) studies, "No failure" and "Failure" points have been plotted in the following chart.
Note :
1) A "failure" point (0.3m, 165dB) is below curve. It is failed on bad welding. No further failure after good welding.
2) Red point are "failure" point and Blue point are "No failure" point
3) May be used for 0.2m < D < 0.9m. Use at risk for D < 0.2m and D > 0.9m
PWL Limit Equation For "D-method"
A PWL limt line has been derived from above data and following equation representing this line.
where
PWLlimit = Maximum allowable PWL at Pipe diameter D meter, (dB)
D = Pipe diameter, (m)
This line may be used to assess potential failure of piping downstream of pressure reducing device. Any point above the line potentially fail on AIV, piping treatment or redesign required to minimise the risk of AIV failure. This will be discussed in future...
Related Topic
- Tips on Succession in FREE Subscription
- Subscribes to FREE Hydrocarbon Processing
Sound Power Level (PWL) is the acoustic energy generated by a pressure reduction device. There are several ways to assess the adequacy of the piping to resist AIV fatigue. One of the way to ensure piping downstream of pressure reducing device sufficiently strong to resist AIV fatigue is to ensure the PWL allowable limit of downstream piping higher than the PWL generated by the pressure reducing device. Refer to "Sound Power Level (PWL) Prediction" for equation in prediction PWL.
A piping will have it stiffness and resistivity against vibration. It is very much subject to piping diameter, material properties, wall thickness, distribution of masses, pipe support, etc. Allowable sound power level and/or dynamic stress of piping can be a measurement of this resistivity of piping against excitation due to AIV. Several allowable PWL curves for piping which derived from different method i.e. "D-method", "D/t-method ", "E-method", etc have been used. Besides PWL related method, there are other method i.e. "Dynamic stress method", "Likelihood of Failure (LOF) method", etc which adopting allowable stress level also been used.
"D-Method"
Based on data available in Carucci & Mueller (1982) studies, "No failure" and "Failure" points have been plotted in the following chart.
Note :
1) A "failure" point (0.3m, 165dB) is below curve. It is failed on bad welding. No further failure after good welding.
2) Red point are "failure" point and Blue point are "No failure" point
3) May be used for 0.2m < D < 0.9m. Use at risk for D < 0.2m and D > 0.9m
PWL Limit Equation For "D-method"
A PWL limt line has been derived from above data and following equation representing this line.
PWLlimit = 156.8 - 9.8 Ln (D)
where
PWLlimit = Maximum allowable PWL at Pipe diameter D meter, (dB)
D = Pipe diameter, (m)
This line may be used to assess potential failure of piping downstream of pressure reducing device. Any point above the line potentially fail on AIV, piping treatment or redesign required to minimise the risk of AIV failure. This will be discussed in future...
Related Topic
- Extra Attention to Common Point and Similarity on AIV Failure
- Piping Excitation When Expose to Acoustic Energy
- Acoustic Induced Vibration (AIV) Fatigue
- Sound Power Level (PWL) Prediction from AIV Aspect
- Several Criteria and Constraints for Flare Network - Piping
- Flow Element (FE) Upstream or Downstream of Control Valve (CV) ?
Wednesday, April 22, 2009
Display problem ? Click HERE
April 22, 2009... Annual EARTH DAY... An effort to inspire appreciation for the earth's environment and awareness of issues that threatening Earth - One and only one where we are now... preserving is responsibility of everyone of us...
Earth Day in March 25, 2009 has called to turn off all non-essential electrical appliance for 60 minutes. Chemical Process Technology would call to minimize paper consumption (Check out world paper consumption). Whenever you just about to print some documents or article in hardcopy... Ask yourself the following questions :
- Why not print and keep in softcopy ?
- Don't print (hardcopy) if it is not absolutely required
- Think twice if you really want to print...
- Continue to ask similar question other than Earth day...
Related Topic
- Earth Hour - Simple Effort Minimise Global Warming
- Serious Efforts In Minimising GreenHouese Effect (GHE) Emission
- Can We Really Stop Greenhouse Effect (GHE) ?
- Is Your Company "Green" Enough ?
- CO2 to Petrol ?
- Methane Conversion Challenge
- Several Concerns in High CO2 Field Development
- Environment related...
Labels: Environment, Global warming, Greenhouse Effect
Tuesday, April 21, 2009
Display problem ? Click HERE
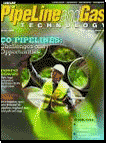
Typical Failure Location
Earlier discussion "Piping Excitation When Expose to Acoustic Energy" has briefly discussed piping segment may be excited in circumferential and longitudinal mode and images showing piping circumferential and longitudinal excitation patterns in different nodal arrangement. Although entire piping system including pipe, welded part, support,tee, etc, previous experiences have shown that typically (not necessarily only) failure occur at the following locations :
- Small bore connection (SBC) i.e. instrument tap, bypass line, etc
- Fabricated Tee
- Welded Pipe support
- Internals i.e. attemporator & inline silencer
Typical Failure System
Based on analysis of data available in Carucci & Mueller (1982) studies and some private communications, following are typical system exprienced failure :
- Compressore anti-surge recycle or Capacity control
- Main Gas Letdown station
- Gas letdown to Flare
- Steam desuperheater
- Small bore connection at large pipe
High Velocity (Mach no)
Another common syntom among failures is piping experiencing sonic flow or choked flow. Whenever sonic flow or choked flow occured, it is expected that flow in the piping has reached it limit. Extremely high turbulence level impacting the piping and results irregular movement of piping. This potentially lead to high frequency of peak-to-peak stress.
Sonic flow with flow limitation will results pressure upstream of choking location increase. As pressure increases, it generate higher density and lead to breakage of sonic flow at choking location. Higher flow is passing the choking location. As the flow is increases, sonic flow form immediately and flow is decreases. Above will results in a "pulsating flow" in the choking location. This "pulsating flow" will occur in very short period, induce additional stress to the piping and increase likelihood of failure. Read more advices in piping related to Mach no.
Although High mach no is one of the main common point among all failure, previous failure cases includes piping with low mach no (Mach no less than 0.3)). Avoiding high velocity is one of the recommendation however it is not ultimate factor in determining failure of piping due to AIV.
Failure Time & Period
One of the common points is the failure occured during start-up and the failure to occur period is range from 5-10 hours to 2-3 months subject to the sound power level and piping condition. Thus, special attention shall be paid during start-up period.
Related Topic
- Piping Excitation When Expose to Acoustic Energy
- Acoustic Induced Vibration (AIV) Fatigue
- Sound Power Level (PWL) Prediction from AIV Aspect
- Several Criteria and Constraints for Flare Network - Piping
- Potential Problem associate with Double NRV in Series within a Line
- Flow Element (FE) Upstream or Downstream of Control Valve (CV) ?
Monday, April 20, 2009
Display problem ? Click HERE
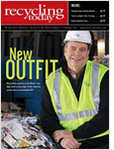
The secret behind this technology is the use of nano-magnets to induce an electromotive force. It uses the same principles as those in a conventional battery, except in a more direct fashion. The energy stored in a battery, be it in an iPod or an electric car, is in the form of chemical energy. When something is turned "on" there is a chemical reaction which occurs and produces an electric current. The new technology converts the magnetic energy directly into electrical energy, without a chemical reaction. The electrical current made in this process is called a spin polarized current and finds use in a new technology called "spintronics.”
Read more in here
Related Topic
- Green Energy : Heat to Electricity
- Power in Human Cell Size Micro Battery
- Tree Power
- Nanowire battery... High Potential of Replacing Lithium Battery
- Fabric Generate Power Caught Global Interests...
- "Power shirt"
Labels: Green Technology, Technology
Tuesday, April 14, 2009
Display problem ? Click HERE
FREE Chemical Engineering Digital Issue for April 2009 has just been released !
Chemical Engineering has just released April 2009 issue. If you are subscriber of Chemical Engineering, you should have received similar notification.
***********************
Interesting articles for this month :
Achema Defies Economic Odds
Even in a recession year, over 180,000 visitors from 100 countries are anticipated at this triennial event
Fingertips Energy Efficiency In Steam Systems
This one-page guide explains the importance of efficient condensate handling in steam systems
Optimizing Pumping Systems
Often overlooked, pump system efficiency makes a dramatic impact on process performance
Calculate Capital Costs Quickly
Estimating capital costs early can prevent wasting money on dead-end projects
Understanding Bends In Pneumatic Conveying Systems
Despite their apparent simplicity, bends are often poorly understood and unless properly designed, they are potentially problematic
***********************
TIPS
If you are subscriber, you may access previous digital releases. Learn more in "How to Access Previous Chemical Engineering Digital Issue".
If you yet to be subscriber of Chemical Engineering, requested your FREE subscription via this link (click HERE). Prior to fill-up the form, read "Tips on Succession in FREE Subscription".
Related Post
- How to Access Previous Chemical Engineering Digital Issue
- Tips on Succession in FREE Subscription
- 3 Most Important & FREE Magazines That I Read...
- Non - Technical Quick References for a Chemical & Process Engineers
- R&D engineer, Academician and Student...Don't miss this !
- More You Share More You Learn
- Knowledge is Own by Everyone but Not Someone
Labels: E-Doc, Education, Learning
Sunday, April 12, 2009
Display problem ? Click HERE
Recommended :

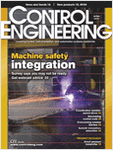
Related Topic
Labels: Emergency Shutdown, Loss Prevention
Saturday, April 11, 2009
Recommended :
Tips on Succession in FREE Subscription
Subscribes to FREE Hydrocarbon Processing
Earlier post "Calculate Wetted Surface Area For Horizontal Vessel With Elliptical Head" has presented an accurate equation may be used to calculate wetted surface area for Horizontal Vessel with Elliptical Head. This post will presented a simplified equation to calculate the wetted surface area. Compare to accurate presented earlier, the difference is within 2%.
Let take the same sketch and example used in earlier post... :
A horizontal pressure vessel with radius R and length L (tan-tan) with liquid height of H, the wetted surface area can be the total wetted surface area of cylindrical section and elliptical head (2 heads).
Tips on Succession in FREE Subscription
Subscribes to FREE Hydrocarbon Processing
Let take the same sketch and example used in earlier post... :
A horizontal pressure vessel with radius R and length L (tan-tan) with liquid height of H, the wetted surface area can be the total wetted surface area of cylindrical section and elliptical head (2 heads).
Wetted Surface Area (Cylindrical section)
Wetted Surface Area for Cylindrical section can be calculated with following equation :
Wetted Surface Area (Elliptical head)
Wetted Surface Area for Elliptical head (one head) can be calculated with following equation :

Example
L = 6m
R = D / 2 = 1.5m
Awet,Cyl = 2LRxAcos[(R-H)/R]
Awet,Cyl = 2x6x1.5xAcos[(1.5-1)/1.5]= 22.16 m2
Awet,Head = [2.178 / (2 x 3.141592654)]x(2x1.5)^2 x Acos[(1.5-1)/1.5] = 3.84 m2
Total wetted surface area, S = Scyl + 2 x Shd = 29.84 m2
Above equations have been programmed by Ankur & Kenny, share with readers of Chemical and Process Technology. You may download here.
Thanks to Ankur & Kenny
Download
*If you have any useful program and would like to share within our community, please send to me.
Related Post
Wetted Surface Area for Cylindrical section can be calculated with following equation :
Wetted Surface Area (Elliptical head)
Wetted Surface Area for Elliptical head (one head) can be calculated with following equation :
where
R = Vessel inside radius (m)
H = Liquid height from bottom (m)
L = Vessel tangent-to-tangent length (m)
R = Vessel inside radius (m)
H = Liquid height from bottom (m)
L = Vessel tangent-to-tangent length (m)
Example
An ellipsoidal heads horizontal vessel with internal diameter (D) of 3m and tangent-tangent length is 6m. Determine wetted surface area when maximum liquid level is at 1m above vessel bottom.
L = 6m
R = D / 2 = 1.5m
Awet,Cyl = 2LRxAcos[(R-H)/R]
Awet,Cyl = 2x6x1.5xAcos[(1.5-1)/1.5]= 22.16 m2
Awet,Head = [2.178 / (2 x 3.141592654)]x(2x1.5)^2 x Acos[(1.5-1)/1.5] = 3.84 m2
Total wetted surface area, S = Scyl + 2 x Shd = 29.84 m2
**********************************
Above equations have been programmed by Ankur & Kenny, share with readers of Chemical and Process Technology. You may download here.
Thanks to Ankur & Kenny
Download
*If you have any useful program and would like to share within our community, please send to me.
Related Post
- Calculate Wetted Surface Area For VERTICAL Cylindrical vessel with Elliptical Head
- Calculate Wetted Surface Area For Horizontal Vessel With Elliptical Head
- PSV for Shell-and-Tube HEX Tube Side Overpressure Protection against External Fire Attack ?
- Should we consider JET FIRE for Pressure Relief Valve (PSV) load determination ?
- Protective Measures against FIRE other than Pressure Relief Device (PRD)
- Extend of Pool Fire...
- Extra Caution When Eliminating Overpressure by Fire Attacks
Thursday, April 9, 2009
Tips on Succession in FREE Subscription
Subscribes to FREE Hydrocarbon Processing
Fire relief estimation for two phase gas liquid in horizontal pressure vessel, wetted surface area is required to estimate total heat input into the horizontal pressure vessel. A horizontal pressure vessel with radius R and length L (tan-tan) with liquid height of H, the wetted surface area can be the total wetted surface area of cylindrical section and elliptical head (2 heads).
Wetted Surface Area (Cylindrical section)
Wetted Surface Area for Cylindrical section can be calculated with following equation :
Wetted Surface Area (Elliptical head)
Wetted Surface Area for Elliptical head (one head) can be calculated with following equation :

Example
L = 6m
R = D / 2 = 1.5m
F = H / 2R = 1 / (2 x 1.5) = 0.333
A = F - 0.5 = 0.333 - 0.5 = -0.167
B = SQRT[1+12A^2] = SQRT[1+12x(-0.167)^2] = 1.1547
Awet,Cyl = 2LRxAcos[(R-H)/R]
Awet,Cyl = 2x6x1.5xAcos[(1.5-1)/1.5]= 22.16 m2
Awet,Head = (PIxR^2/2)x[AxB+1+1/(4e)xLn[((4exA)+B)/(2-3^0.5)]=3.64 m2
Total wetted surface area, S = Scyl + 2 x Shd = 29.43 m2
Ref : "Accurate Wetted Areas for Partially Filled Vessels", by Richard C. Doane, "Chemical Engineering", December 2007
Above equations have been programmed by Ankur, a experience Chemical Engineer, share with readers of Chemical and Process Technology. You may download here.
Thanks to Ankur
Download
*If you have any useful program and would like to share within our community, please send to me.
Related Post
Wetted Surface Area for Cylindrical section can be calculated with following equation :
Wetted Surface Area (Elliptical head)
Wetted Surface Area for Elliptical head (one head) can be calculated with following equation :
where
R = Vessel inside radius (m)
H = Liquid height from bottom (m)
L = Vessel tangent-to-tangent length (m)
e (epsilon) = Eccentricity (0.866 for 2:1 Ellipsoidal head)
F = Fraction Liquid Level, = H / 2R
R = Vessel inside radius (m)
H = Liquid height from bottom (m)
L = Vessel tangent-to-tangent length (m)
e (epsilon) = Eccentricity (0.866 for 2:1 Ellipsoidal head)
F = Fraction Liquid Level, = H / 2R
Example
An ellipsoidal heads horizontal vessel with internal diameter (D) of 3m and tangent-tangent length is 6m. Determine wetted surface area when maximum liquid level is at 1m above vessel bottom.
L = 6m
R = D / 2 = 1.5m
F = H / 2R = 1 / (2 x 1.5) = 0.333
A = F - 0.5 = 0.333 - 0.5 = -0.167
B = SQRT[1+12A^2] = SQRT[1+12x(-0.167)^2] = 1.1547
Awet,Cyl = 2LRxAcos[(R-H)/R]
Awet,Cyl = 2x6x1.5xAcos[(1.5-1)/1.5]= 22.16 m2
Awet,Head = (PIxR^2/2)x[AxB+1+1/(4e)xLn[((4exA)+B)/(2-3^0.5)]=3.64 m2
Total wetted surface area, S = Scyl + 2 x Shd = 29.43 m2
**********************************
Above equations have been programmed by Ankur, a experience Chemical Engineer, share with readers of Chemical and Process Technology. You may download here.
Thanks to Ankur
Download
*If you have any useful program and would like to share within our community, please send to me.
Related Post
- Calculate Wetted Surface Area For VERTICAL Cylindrical vessel with Elliptical Head
- Calculate Wetted Surface Area For HORIZONTAL Vessel With Elliptical Head (Simplified)
- PSV for Shell-and-Tube HEX Tube Side Overpressure Protection against External Fire Attack ?
- Should we consider JET FIRE for Pressure Relief Valve (PSV) load determination ?
- Protective Measures against FIRE other than Pressure Relief Device (PRD)
- Extend of Pool Fire...
- Extra Caution When Eliminating Overpressure by Fire Attacks
Wednesday, April 8, 2009
Display problem ? Click HERE
Recommended :
- Subscribe FREE - Chemical Engineering
- Tips on Succession in FREE Subscription
ChemicalProcessing.com has conducted annual salary survey from 2005, to 2009. Survey show that average salaries have steadily increased from 2005 to 2009. Average salaries started with $85,234 in 2005, increased to $89,690 in 2006, $90,038 in 2007, $95,231 in 2008 and lately $107,804 in 2009. However, the average pay raise was down slightly, 4.23% compared to the 5.06% reported in 2008. Details of these surveys may refer to :
Thanks to Ken Schnepf, Managing Editor of Chemical Processing.
Related Post
- 2005 Chemical Industry Salary Survey
- 2006 Chemical Industry Salary Survey
- 2007 Chemical Industry Salary Survey
- 2008 Chemical Industry Salary Survey
- 2009 Chemical Industry Salary Survey
Thanks to Ken Schnepf, Managing Editor of Chemical Processing.
Related Post
Display problem ? Click HERE
The objective of this talk is to provide an overview of the phases of a project along with the project management controls necessary for the successful management of HSE as applicable to E&P type projects. It will describe the specific applications of Hazards and Risk Management tools at key stages of the project and will review how the ALARP target factors in on major project conceptual and detailed design decisions and direction.
The talk will focus, on various project stages and the relevant HSE objectives, tools and techniques that typically are employed to achieve the desired objectives and the deliverables expected at the end of each stage. It will also provide pointers to more detailed references and guidance for their application. It is not the intention of this talk to provide a complete specification of the HSE activities to be undertaken at each stage of a project. Nonetheless, it will provide guidance on key activities that need to be considered by those responsible for project design.
A talk on "HSE in projects - Focusing on design", organized by Oil, Gas & Mining Technical Division, IEM has been scheduled.
Date : 13 April 2009 (Monday)
Time : 5.30 pm to 7.00 pm
CPD : 2 Hours (approved by BEM)
Venue : Wisma IEM (New Building), Petaling Jaya
Speaker : Mr. Christopher James Bernard (CJB
*Any queries, please contact sec@iem.org.my.
Related Post
Labels: Environment, iem, NEWS
Monday, April 6, 2009
Display problem ? Click HERE
Recommended :
- Subscribe FREE - Processing Magazine
- Tips on Succession in FREE Subscription
Earlier discussion in "Acoustic Induced Vibration (AIV) Fatigue" has discussed the generation of high frequency acoustic excitation downstream of pressure reducing device and potential of downstream piping failure due to Acoustic Induced Vibration (AIV). Acoustic energy can lead to circumferential and longitudinal excitation. Read more in "Piping Excitation When Expose to Acoustic Energy" to see how piping is excited by acoustic energy. Piping downstream of pressure reducing device shall be designed sufficiently strong to resist AIV fatigue. One of the common acceptable criteria to indicate piping resistivity to AIV fatigue is ensuring Sound Power Level (PWL) allowable limit of downstream piping higher than the PWL generated by the pressure reducing device.
- Subscribe FREE - Processing Magazine
- Tips on Succession in FREE Subscription
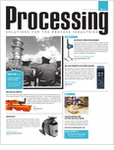
Sound Power Level Generated by Pressure Reducing Device
Acoustic energy generated by a pressure reducing device may range from 0 to 10 MW. It is more convinient to express this energy in another term called Sound Power Level (PWL) in logarithmic scale with reference to a most common acceptable reference power of 10^(-12) watts (W). Thus, PWL is 10 times the logarithm to the base 10 of the ratio of acoustic enerygy to reference power of 10^(-12) watts. A common acceptable method to predict Sound Power Level (PWL in dB) is as follow :
Example
A Depressuring valve open to pass 100,000 kg/h of gas with molecular weight (MW) of 22. The inlet condition is 87 barg and 50 degC and estimated backpressure is about 7 barg.
PWL = 10 x Log [((87-7) / (87+1.01325))^3.6
x (100,000 / 3600)^2
x ((50+273.15)/22)^1.2]
+ 126.1
PWL = 167.5 dB
Allowable Sound Power Level (PWL) of Piping
A piping will have it stiffness and resistivity against vibration. It is very much subject to piping diameter, material properties, wall thickness, distribution of masses, pipe support, etc. Allowable sound power level and/or dynamic stress of piping can be a measurement of this resistivity of piping against excitation due to AIV. Several allowable PWL curves for piping which derived from different method i.e. "D-method", "D/t-method ", "E-method", etc have been used. Besides PWL related method, there are other method i.e. "Dynamic stress method", "Likelihood of Failure (LOF) method", etc which adopting allowable stress level also been used. This may be discussed in future post.
Ref :
i) "Designing Piping Systems Against Acoustically Induced Structural Fatigue", E.L. Eisinger, Journal of Pressure Vessel Technology, Aug 1997.
Related Topic
Acoustic energy generated by a pressure reducing device may range from 0 to 10 MW. It is more convinient to express this energy in another term called Sound Power Level (PWL) in logarithmic scale with reference to a most common acceptable reference power of 10^(-12) watts (W). Thus, PWL is 10 times the logarithm to the base 10 of the ratio of acoustic enerygy to reference power of 10^(-12) watts. A common acceptable method to predict Sound Power Level (PWL in dB) is as follow :
Example
A Depressuring valve open to pass 100,000 kg/h of gas with molecular weight (MW) of 22. The inlet condition is 87 barg and 50 degC and estimated backpressure is about 7 barg.
PWL = 10 x Log [((87-7) / (87+1.01325))^3.6
x (100,000 / 3600)^2
x ((50+273.15)/22)^1.2]
+ 126.1
PWL = 167.5 dB
Allowable Sound Power Level (PWL) of Piping
A piping will have it stiffness and resistivity against vibration. It is very much subject to piping diameter, material properties, wall thickness, distribution of masses, pipe support, etc. Allowable sound power level and/or dynamic stress of piping can be a measurement of this resistivity of piping against excitation due to AIV. Several allowable PWL curves for piping which derived from different method i.e. "D-method", "D/t-method ", "E-method", etc have been used. Besides PWL related method, there are other method i.e. "Dynamic stress method", "Likelihood of Failure (LOF) method", etc which adopting allowable stress level also been used. This may be discussed in future post.
Ref :
i) "Designing Piping Systems Against Acoustically Induced Structural Fatigue", E.L. Eisinger, Journal of Pressure Vessel Technology, Aug 1997.
Related Topic
- Piping Excitation When Expose to Acoustic Energy
- Acoustic Induced Vibration (AIV) Fatigue
- Several Criteria and Constraints for Flare Network - Piping
- Potential Problem associate with Double NRV in Series within a Line
- Flow Element (FE) Upstream or Downstream of Control Valve (CV) ?
- Why a globe valve is located downstream of manual block valve on drain line ?
- How to Select a Check Valve (NRV) Quantitatively ?
- Why bypass Non-Return Valve (NRV) ?
Saturday, April 4, 2009
Display problem ? Click HERE
Recommended :
- Subscribe FREE - Processing Magazine
- Tips on Succession in FREE Subscription
Earlier discussion in "Acoustic Induced Vibration (AIV) Fatigue" has discussed the generation of high frequency acoustic excitation downstream of pressure reducing device and potential of downstream piping failure due to Acoustic Induced Vibration (AIV). Whenever there is pressure drop with mass passing through the valve, internal acoustic energy is generated and transmitted to downstream piping and potentially lead to severe piping excitation, vibration and stresses on downstream piping, in particular at discontinuity section i.e fabricated Tee, small bore connection, welded pipe and pipe support, etc. This acoustic excitation phenomena is generally involve high frequency (more than 1000Hz) acoustic energy. When high frequency acoustic energy is matches with mechanical natural frequency of piping and its component, excitation amplitude is at maximum and lead to increased stress level.
A piping segment may be excited in circumferential and longitudinal mode. Following image shows piping circumferential and longitudinal excitation patterns in different nodal arrangement.
The following video clip shown a piping excitation in circumferential and lead to severe stress level at branch.
Related Topic
- Subscribe FREE - Processing Magazine
- Tips on Succession in FREE Subscription
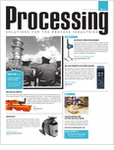
A piping segment may be excited in circumferential and longitudinal mode. Following image shows piping circumferential and longitudinal excitation patterns in different nodal arrangement.
The following video clip shown a piping excitation in circumferential and lead to severe stress level at branch.
Related Topic
- Acoustic Induced Vibration (AIV) Fatigue
- Sound Power Level (PWL) Prediction from AIV Aspect
- Several Criteria and Constraints for Flare Network - Piping
- Potential Problem associate with Double NRV in Series within a Line
- Flow Element (FE) Upstream or Downstream of Control Valve (CV) ?
- Why a globe valve is located downstream of manual block valve on drain line ?