Sunday, March 15, 2009
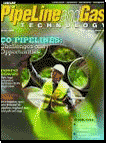
In earlier post "Several Criteria and Constraints for Flare Network - Process", several major important criteria and constraints have been discussed. They includes Mach number, back pressure, noise level and two phase flow pattern. This post is the continuation and futher discuss other criteria and constraints for flare networt.
Flow Induced Vibration (FIV)
In a process plant, some of pressure control valves (PCV) may be provided in the process system to release gas into flare network to avoid transient peak pressure in the process system which potentially lead to unnecessary plant shutdown. Besides, this PCV may be used to release off specification gas into flare during plant start-up. Above events will increase the operational time of the PCV and its downstream piping and increase the piping Likelihood of Failure (LOF) due to flow induced vibration (FIV). Typically these PCV would experience low frequency exitation. It is good engineering practice to ensure the
- LOF2 < 0.3 + Good engineerng practice for Small Bore Connection (SBC) or;
- 0.3 <= LOF2 < 0.5 +LOF3 < 0.4
LOF3 is Likelihood of Failure for small bore connection
Acoustic Induced Vibration (AIV)
Pressure control valve (PCV) with choking condition, pressure relief valve (PRV) and Blowdown valve with restriction orifice (BDV/RO) provided in the process and relief to flare network would cause high frequency acoustic exitation to downstream piping and potential results piping failure on Acoustic Induced Vibration (AIV). If the PWL generated by these devices is below PWL lower than 155 dB, the piping downstream of these devices are considered safe from AIV fatigue failure.
Piping downstream of these device may have different wall thickness. Piping with higher wall thickness will be more likely to resist higher PWL. Based on field experiences, table below list the maxmum limit of PWL with increasing ratio of Outside diameter (OD) to wall thickness (wt).
Limit of PWL vs OD/wt | |
OD / wt | PWL,max |
20 | 174 |
30 | 173 |
40 | 172 |
50 | 170 |
60 | 169 |
70 | 168 |
80 | 167 |
90 | 165 |
100 | 164 |
110 | 163 |
120 | 162 |
130 | 160 |
140 | 159 |
150 | 158 |
Above is the PWL limit , some margin i.e. 3 dB may need to be added.
Maximum and Minimum Design Temperature and Thermal Shock
A flare network maximum and minimum design temperature will be typically determine from fluid discharging into the flare network. The maximum design temperature would typicall determine based on maximum possible fluid temperature with margin (plus) i.e. 10 degC whilst the minimum design temperature would typically determine from minimum fluid temperature with margin (minus) i.e. -10 degC or the fluid minimum depressured temperature with no or lower magin i.e. - 5 degC. The flare network potentially expose to high temeperature fluid during normal plant operaion and follow by cold fluid discharge from process system. Sudden large temeprature decrease in piping may cause thermal shock. Thus, flare piping stress shall analysed base on worst possible and credible temperature different and ensure sufficient expansion loops are provided and proper location of support.
Slug Hammer Elbow
For flare network piping identify potentiall expose to slugging condition, beside provision of necessary support, the slug hammering elbow is potential event and needs to further analyse the impact of the slug hammer.
Solidification, Crystillization, Polymerization, Hydrate and/or Ice Formation
Relief fluid believe to solidify, crystallize and/or polymerize, it potentially plug / block the relief tail pipe and flare network. Further analysis shall be conducted to check should these fluids be discharged in to the flare network. Possible solution is discharge to separate and dedicated disposal drum and vent.
For some flare network receiving wet fluid from high pressure system i.e. slugcatcher, theoretically there is potential of hydrate formation. However, due to high velocity, warm flare piping, intermittent service and non-sustainable discharge flow, field experience shows the likelihood of hydrate formation in flare network is low. Having said that additional measures shall be taken in to consideration. Read more in "Hydrate formed Downstream of PRV ?".
Other issue such as correct material for discharge fluid, corrosion and stress cracking, fluid compatibility studies, etc are those studies have been conducted and decided prior to flare network analysis. Thus, they are not discuss further in this post.
Concluding Remark
Previous post "Several Criteria and Constraints for Flare Network - Process" have discussed those criteria and constraints typically for process aspect whilst this post are typically from piping aspect. All criteria and constrains are listed as follow :
- Mach no
- Momentum
- Back pressure
- Noise
- Two phase flow pattern
- Flow Induced Vibration
- Acosutic Induced Vibration
- Thermal Shock
- Slug Hammering
- Hydrate / Ice Formation
Related Topic
0 Comments:
Post a Comment
Let us know your opinion !!! You can use some HTML tags, such as <b>, <i>, <a>
Subscribe to Post Comments [Atom]
Home:
<< Home