Sunday, February 22, 2009
Display problem ? Click HERE
Recommended :
- Tips on Succession in FREE Subscription
- Subscribe FREE - Processing Magazine
American Petroleum Petroleum (API) released the ANSI / API Std 537 / ISO 25457:2008 "Flare Details For General Refinery and Petrochemical Service" Second Edition, Dec. 2008 in December 2008. First important change is it has been upgraded as ISO compliance. User shall remember although it is a standard, it is solely users responsibility to make sound, scientific, engineering, safe, environment friendly judgment. Neither API nor its employee, etc make warranty for the use of this standard. Detail refer to "Special Note" in relevant Standard.
Applicability- Tips on Succession in FREE Subscription
- Subscribe FREE - Processing Magazine
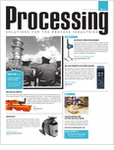
User of this standard shall understand the applicability of this standard. This standard specifies requirements and provides guidance for the selection, design, specification, operation and maintenance of flares and related combustion and mechanical components used in pressure relieving and vapour-depressurizing systems for petroleum, petrochemical and natural gas industries. It is primarily intended for new flares and related equipment, it may be used to evaluate existing flare facilities.

Recommended :
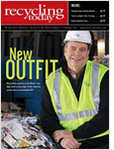
API Std 537 / ISO 25457 is primarily to provide mechanical related information related to flare. For flare system design and related criteria and limitation, user may refer to API Std 521 / ISO 23251 "Pressure Relieving and Depressuring System".
There are several important information that a process engineers may take note :
- A simple flowchart for Flare Type Selection has been included in this new standard. This flowchart will provide a quick way to understand the potential flare tip type may be selected by the flare vendor. Read more in "Flare Tip Quick Selection Chart"
- Larger the flare tip diameter, more number of pilots is required. The following table provide minimum requirement of pilots for flare burner diameter. This table presented a minimum pilots per burner, one shall remember there is possibility of pilot, mixer, ignition, etc fail. Thus, redundancy / spare shall be provided.
Flare burner outlet diameter (DN) | Flare burner outlet diameter (NPS) | Minimum number of pilots | Note |
Up to 200 | Up to 8 | 1 | (1) |
>200 to 600 | >8 to 24 | 2 | |
>600 to 1050 | >24 to 42 | 3 | |
>1050 to 1500 | >42 to 60 | 4 | |
>1500 | >60 | - | (2) |
(1) For toxic gas, the minimum number shall be two.
(2) To be agreed with the purchaser.
- Minimum pilot fuel gas consumption is 13.2 kW (45000 btu/h). Knowing the Lower/Net heating value of fuel gas, the minimum pilot gas consumption per pilot can be determined. Together with above information, a process engineer may estimate continuous fuel gas consumption for all pilot
- This standard recommends a minimum corrosion allowance of 1.6 mm (1/16") to be provided for carbon steel riser contact with relief fluid.
- Smokeless flaring is normally achieved by utilizing air, steam, water, pressure energy, etc. The requirement of smokeless flaring is determine by local authority or company requirements. Ringlemann number is used for the definition of smokeless level. Read more related to Ringlemann chart in "Flare Smokeless Ringlemann Chart".
- Minimum LHV of 7450 kJ/Nm3 (200 Btu/scf) for unassisted flare whilst 11175 kJ/Nm3 (300 Btu/scf) for assisted flare (Ref.: 40 CFR PT 60.18). This may be applicable to normal pipe flare. For sonic flare tip, a higher LHV value i.e 800 BTU/scf (subject to vendor) may be required.
- As highlighted, a steam assisted flare, noise level is the combination of combustion noise and steam jet noise, typically high. Additional attention is required for steam and water assisted flare.
- For low ambient (subzero during winter), there is potential partial/total blockage of steam/water header due to ice formation. Additional attention is required for steam and water assisted flare.
- There are typical Flare Tip datasheet available in this standard which assist purchaser, contractor and manufacturer in proper communication of information.
To find details of API Standard 537/ISO 25457, please check out here
For those would like to read more about brief information about the background, intention, contents, structure, etc related to this standard, you may read "New API Standard provides comprehensive information on flares" by R. SCHWARTZ
For those would like to read more about brief information about the background, intention, contents, structure, etc related to this standard, you may read "New API Standard provides comprehensive information on flares" by R. SCHWARTZ
Download
Source : JohnZink
Related Topic
- Flare Smokeless Ringlemann Chart
- Guideline on Quick Determination of Flare Stack Support Type
- Must Read Flare Handbook
- Steam in FIRE...
- Why not bury flare pipe header ?
- Use Ultra-Sonic Flowmeter in FLARE Gas Header for emission monitoring
- FLARE combustion efficiency
- Factors and Criteria for Vent Stack Design
Labels: Combustion, Flare
0 Comments:
Post a Comment
Let us know your opinion !!! You can use some HTML tags, such as <b>, <i>, <a>
Subscribe to Post Comments [Atom]
Home:
<< Home