Wednesday, November 28, 2007
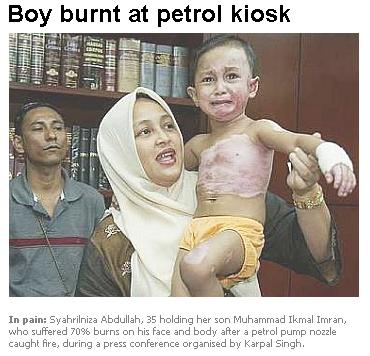
Today i read a news here "Boy burnt at petrol kiosk". Pity the boy with 70% burnt on his face and body. The victim mentioned the following :
"As I pulled the pump nozzle out from the petrol tank, it caught fire.
"Fuel was still coming out from the burning nozzle and then adik was on fire. I threw the nozzle down and started rolling him on the ground to put out the fire."
"He said he shouted for the fire extinguisher twice but it took a while for the station staff to get it as it was locked in the office. "
"He said he shouted for the fire extinguisher twice but it took a while for the station staff to get it as it was locked in the office. "
From the story, i have noticed two major points
CAUSES
There are many causes can lead to ignition of petrol :
SECURITY
Fire extinguisher is meant for emergency use but yet it store and locked in the office for security reason.
ADVICES
This has triggered me to think more as we are dealing with this on daily basis.
- fire started spontaneously without any cause.
- fire extinguisher is locked in the office.
CAUSES
There are many causes can lead to ignition of petrol :
- Static charge - Some clothing may easily generate static electric when people moves. It can cause petrol fume ignited.
- Cell phone - it carry battery and may send and receive signal without people knowing. It is another potential cause ignition. This worst could be cell phone ring when you are filling the petrol. READ more HERE.
- Fill petrol without shutting car engine - Car engine is hot and continuously generating heat. Exhaust gas is hot may poses risk of petrol ignition.
- Smoking - This is an obvious cause. Nobody is allowed to smoke at petrol station. Sometime the problem may came from ignorance and uneducated attendant. READ more HERE.
SECURITY
Fire extinguisher is meant for emergency use but yet it store and locked in the office for security reason.
- Ignorance - The owner and attendant ignore safety rule and regulation.
- Uneducated - Many attendant are from non-educated group. They may not aware of safety concern
ADVICES
This has triggered me to think more as we are dealing with this on daily basis.
- Static charge - Sometime you can not avoid generation of static charge but you can "discharge" it. Touch metal or structure before you take the petrol nozzle out from the holder. It helps to discharge (partly if not fully) the static charge.
- Cell phone - Never take the cell phone with you in the petrol station. Keep it in the car. Also don't answer any call. If possible, switch it off.
- Fill petrol without shutting car engine - Stop the engine.
- Smoking - I guess this is well aware by all of us but please don't ignore.
- Locked Fire Extinguisher - i would say make a report to authority and leave it to the enforcement team. NEVER goes back to this station again.
- Educate those you love - You are probably serving Chemical and Process or Oil and Gas community. You are partly the "expert" in front of others. Educate others...they will believe it base on your credibility.
Labels: Accident, Loss Prevention
Tuesday, November 27, 2007
Control valve has been widely used in Chemical & Process Plant for material feeding control and operating condition control, material feeding control. Today control valve technology is highly reliability and availability and long life span. It is a very mature technology. There are many handbooks and articles available online and FREE for read and download. Out of all, i would like to highlight a few that i think they are rather complete and you shall not miss them.
FISHER CONTROL VALVE HANDBOOK
Emerson Fisher
The Control Valve Handbook is both a textbook and a reference on the strongest link in the control loop, the control valve and its accessories. This book includes extensive and proven knowledge from leading experts in the process control field including contributions from the ISA and the Crane Company...
MASONEILAN CONTROL VALVE HANDBOOK
Masoneilan
This handbook on control valve sizing is based on the use of nomenclature and sizing equations from ISA Standard S75.01 and IEC Standard 534-2. Additional explanations and supportive information are provided beyond the content of the standards...
GUIDELINES FOR APPLICATION OF CONTROL VALVES
Process Industrial Practices
In an effort to minimize the cost of process industry facilities, this Practice has been prepared from the technical requirements in the existing standards of major industrial users, contractors, or standards organizations. By harmonizing these technical requirements into a single set of Practices, administrative, application, and engineering costs to both the purchaser and the manufacturer should be reduced. While this Practice is expected to incorporate the majority of requirements of most users, individual applications may involve requirements that will be appended to and take precedence over this Practice...
VALVE SIZING & SELECTION
CheResources
Step-by-step control valve sizing method and comparison of different types of control valve as well as selection...
CONTROL VALVE TUTORIAL
Spirax Sarco
This tutorial briefly describes the basic components of different types of linear and rotary action control valves available for use in steam and water systems...
SIZING AND SELECTION OF CONTROL VALVES
Siemens
The control valve is the most important single element in any fluid handling system, because it regulates the flow of fluid to the process. To properly select a control valve, a general knowledge of the process and components is usually necessary. This reference section can help you select and size the control valve that most closely matches the process requirements. The sizing of a valve is very important if it is to render good service. If it is undersized, it will not have sufficient capacity. If it is oversized, the controlled variable may cycle, and the seat, and disc will be subject to wire drawing because of the restricted opening.
EASE CONTROL VALVE SELECTION
With so many types and options available, choosing the right control valve can seem daunting. Selection can be simplified by considering the process fluid, the service requirements, and how the various valves function.
PLANT DESIGN & CONTROL VALVE SELECTION UNDER INCREASING COST & TIME PRESSURE
Dipl. Ing. Holger Siemers, SAMSON AG
- (Part I) - This article is split into two parts: broadly speaking, part one looks at control valve operating points and provides a case history involving a mismatch. The author introduces better valve sizing practices and uses this theory to resolve the problems introduced in the case history. Part two (scheduled for the June issue) starts by explaining the trends and definitions of inherent valve characteristics before focusing on, "quick and dirty" sizing. The paper then addresses cavitation before concluding with the expert software CONVAL to help select the optimum valve characteristic form.
- (Part II) - Part two starts by explaining the trends and definitions of inherent valve characteristics before focusing on "quick and dirty" sizing. The paper then addresses cavitation before concluding with the expert software available to help select the optimum valve characteristic form.
CONTROL VALVE DESIGN ASPECTS FOR CRITICAL APPLICATIONS IN PETROCHEMICAL PLANTS
Dipl. Ing. Holger Siemers, SAMSON AG
- (Part I) - This paper reviews the past, present and future of valve design and sizing, taking all-important issues such as increasing cost pressure and time pressure into account. This paper is presented in two parts: firstly, how to use manufacturer independent software to analyze given or calculated plant parameters in more detail from an overall point of view with a complete power check and optimizing possibilities. Some case studies are also discussed. The second section, scheduled for a future issue, includes information on to design, size and use severe service control valves with good performance for long maintenance intervals. Different philosophies of valve design (plug design), pressure balance systems, stem sealing, actuator sizing, cost philosophies for "high end" applications are discussed.
- (Part II) - This section presents information on design, size and use of severe service control valves, the kind of troubles that can be predicted with control valve sizing as well as suggestions for troubleshooting control valve failures.
- (Part III) -...Continue from (Part II)
WARREN CONTROLS
A Control Valve performs a special task, controlling the flow of fluids so a process variable such as fluid pressure, fluid level or temperature can be controlled. In addition to controlling the flow, a control valve may be used to shut off flow. A control valve may be defined as a valve with a powered actuator that responds to an external signal. The signal usually comes from a controller. The controller and valve together form a basic control loop. The control valve is seldom full open or closed but in an intermediate position controlling the flow of fluid through the valve. In this dynamic service condition, the valve must withstand the erosive effects of the flowing fluid while maintaining an accurate position to maintain the process variable.
WELKER JET CONTROL VALVE - A PRACTICAL APPLICATION HANDBOOK
Welker Eng
The current Welker Jet® and the earlier Jet Stream™ Control Valves are the most unique Control Valves on the market today. Over the last 44 years, Welker employees have discussed the Jet with thousands of people and users in over 15 countries worldwide. Because of its unique features and unparalleled performance, much has been said and misunderstood about this product. In an attempt to clarify some of these statements and to share the accumulated "pearls of wisdom" that have been recorded over the years, this handbook has been assembled. A full understanding of the Jet, will give the engineer, designer, operations personnel and technician a greater appreciation for the features that the Jet presents and the performance that can be expected. The Jet can solve many problems that otherwise would create additional engineering and cost for the gas company.
FAQ Related to Control Valves
Besides theory and practical knowledge in articles, there are still many frequently asked questions related to control valve. Following is a list of frequently asked question (FAQ) related to control valve. It is pretty useful especially to young engineer.
MY WISH...
I have received number of emails from sincere reader of this blog. Large percentage are came from young and dynamic engineers. They are willing to learn and contribute within our community. Above is only part of many that i think are useful for a young engineers. I hope you may learn from them. Also if you know any that is useful...please let me know. I will pack here for the benefits of all...
(updated on Feb 07, 2008)
Related Topic
- Hydraulic Design Of Liquid with Pump Circuit - A revision kit...
- Hydraulic Design of Liquid Piping Systems - A revision kit...
- Why bypass Non-Return Valve (NRV) ?
Labels: Control valve, Ebook, Learning
Saturday, November 24, 2007
Finally i have completed my compilation of previous posts... For those who has not read my previous posts, you may enjoy reading them now.
CATEGORY sort by ALPHABET & CATEGORY
POST per CATEGORY sort by ALPHABET A
POST per CATEGORY sort by ALPHABET B
POST per CATEGORY sort by ALPHABET C
POST per CATEGORY sort by ALPHABET D
POST per CATEGORY sort by ALPHABET E
POST per CATEGORY sort by ALPHABET F
POST per CATEGORY sort by ALPHABET G
POST per CATEGORY sort by ALPHABET H
POST per CATEGORY sort by ALPHABET I
POST per CATEGORY sort by ALPHABET J
POST per CATEGORY sort by ALPHABET L
POST per CATEGORY sort by ALPHABET M (updated Nov 24, 2007)
POST per CATEGORY sort by ALPHABET N (updated Nov 24, 2007)
POST per CATEGORY sort by ALPHABET O (updated Nov 24, 2007)
POST per CATEGORY sort by ALPHABET P (updated Nov 24, 2007)
POST per CATEGORY sort by ALPHABET R (updated Nov 24, 2007)
POST per CATEGORY sort by ALPHABET S (updated Nov 24, 2007)
POST per CATEGORY sort by ALPHABET T (updated Nov 24, 2007)
POST per CATEGORY sort by ALPHABET U (updated Nov 24, 2007)
POST per CATEGORY sort by ALPHABET V (updated Nov 24, 2007)
POST per CATEGORY sort by ALPHABET W (updated Nov 24, 2007)
POST per CATEGORY sort by ALPHABET Y (updated Nov 24, 2007)
Labels: General
Thursday, November 22, 2007
Display problem ? Click HERE
Heuristic is method, tricks & tips that common used to helps in approaching a problem. It is a compilation of knowledges and experiences by most (if not all) individual. It helps to tackle problem in a simple, reasonable and generally optimized ways and to avoid repetitive common failure.
Similar to other sectors and disciplines, most credible Chemical and Process Engineers have put a lot of efforts in compilation of their knowledges, experiences, etc and produced Heuristic dedicated to Chemical & Process Engineering...
In my process design career, i have found two most credible and reliable Heuristic in Chemical & Process Engineering.
"Although experienced engineers know where to find information and how to accurate computations, they also keep a minimum body of information in mind on the ready, made up largely of shortcuts and heuristics. the present compilation may fit into such a minimum body of information, as boost to memory or extension in some instances into less often encountered areas."
"Experience is typically what turns a good engineer into a greater engineer. An engineer that can look at a pipe and a flowmeter and guess the pressure drop within 5%. Someone who can at least estimate the size of a vessel without doing any calculations. When I think of such rules, two authors come to my mind, Walas and Branan. Dr. Walas' book, Chemical Process Equipment: Selection and Design has been widely used in the process industry and in chemical engineering education for years. Mr. Branan has either helped write or edit numerous books concerning this topic. Perhaps his most popular is Rules of Thumb for Chemical Engineers. areas."
These articles are available FREE for all in our community. If you don't aware of these articles, please read them. I am sure that you will benefits in the future Chemical & Process Engineering career.
My 2-cents advice
One shall always keep in mind that these articles are the best effort by most credible engineers. The heuristic and recommended rule of thumbs are experience and case specific. It is NOT some compulsory rule that we needs to comply to. It provides guideline to approach problem but engineering judgment and detailed calculation and design shall be conducted for final confirmation.
Last but not least, please rate this article and provide your valuable comments. Your 10 second of effort worth million to me...
Further Reading :
Labels: Education, Learning, Rule-Of-Thumb
Tuesday, November 20, 2007
This post is for those use ASPENTECH HYSYS 2006 release...
New bug found in ASPENTECH HYSYS Dynamic Depressuring unit, [Fisher] Valve model...
Incident
The peak flow is higher when [Fisher] valve model under valve parameters in Dynamic depressuring Utility is selected.
Cause
There is a problem with the Fisher equation calculation in the 2006 dynamic tool. A disproportionate scale term in the equation has been used such that it causes wrong Cv and peak flow calculation.
Workaround
Workaround
There is no workaround for time being and will be fixed in 2006.5 version, expected to be released in Jan 2008.
SourceThis information has been informed by Kandan (nickname) and further advised by dyogal (nickname). I have finally got the confirmation from ASPENTECH via my personal account ( Incident no. 886087).
Updated on Oct 22, 2007
This bug only occurs in ASPENTECH HYSYS version 2006. They are fine in other vision such as 3.1, 3.2, 2004.1 and 2004.2.Updated on Oct 22, 2007
Further Reading :
- Another descrepancy found in API Std 521Jan 2007
- Controlled and Non-controlled Type Depressuring.
- How to apply valve equation in HYSYS Depressuring ?
- 6 elements & factors lead to high quality question
- Carefully assess information in the web
- 12 Features required for Shutdown Valve (SDV)
Labels: Depressurization, Design, HYSYS
Sunday, November 18, 2007
Have you ever heard about Eng-Tips? I guess many of you may aware of this website. Eng-Tips is providing a platform for all engineering professional to raise and discuss real world engineering issue. There are many forums in Eng-Tips which stretch from Aeronautical, Chemical, Mechanical, Civil, etc. It basically covers almost all the engineering division. Eng-Tips promote engineering professionalism and it manage to pull most credible engineers worldwide discuss critical engineering issues and share knowledge and experiences among engineers within a community. I have been reading interesting posts in several forums on daily basis for past 1 year without failed. Because I am certain that I can gain a lot of information, knowledge, insights, experiences, etc from other experienced engineers through Eng-Tips.
If you are practicing engineer…
- and if you don’t aware of this website, check it out HERE…
- and If you have not registered to this website, I would encourage you to register…HERE
I don’t think you will regret with your registration to this website.
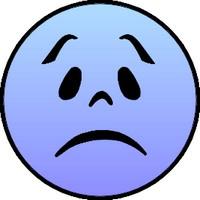

Until one nice morning, I received a note from Latexman. He is willing to assist me in the registration. Finally, I have succeeded in registration to Eng-Tips. I really appreciate Latexman's assistance…I am really respect Latexman…read him HERE.
One of major factor contributes to my succession in registration is my consistence and progressive contribution to our society & community specifically via CheResources Forum.
One of major factor contributes to my succession in registration is my consistence and progressive contribution to our society & community specifically via CheResources Forum.
My successful handle in Eng-Tips is JoeWong88. From my profile, you can see that this Eng-Tips has been in the record since Jan 09, 2007. Well…I only manage to login last week. I also would like to thank the Eng-Tips to take extra effort to activate my account. From now on, I can raise question and contribute my 2-cents worth knowledge…
Lesson learned from my unique experience :
Lesson learned from my unique experience :
- You will be compensated if you continue to contribute to the society and community...it is just a matter of time...
- All works and efforts shall be consistence, persistence and continues without failure
- Nothing is free and comes easily without effort
- There are peoples watching you for all your works
Friday, November 16, 2007
Today i have made more compilation for my previous posts.
If you have any suggestion or observation, please let me know.
POST per CATEGORY sort by ALPHABET G
POST per CATEGORY sort by ALPHABET H
POST per CATEGORY sort by ALPHABET I
POST per CATEGORY sort by ALPHABET J
POST per CATEGORY sort by ALPHABET L.
Previous compilation...
Labels: General
Thursday, November 15, 2007
There are many real life experiences have shown that if valves are not work for substantial period, they can stick in the preset position. Past experiences also showed that once it is stuck at one position, system may experience difficulties to move from preset position and sometime failed to move it. Valve sticking / stuck at preset position could be cause by dirt accumulation, corrosion debris, corroded shaft break, etc.
On the hand, valves continuous move from one position to another position (e.g. full close to full open and vice versa) will minimize the chances of dirt and corrosion debris accumulation and get harden. A continuous moving valve with constant monitoring of it stroking time will enable alert of a out perform valve.
Partial stroke test is one of the testing procedures to ensure reliability and availability of valves. Normally the test is required for critical valve such as battery limit Emergency Shutdown Valves (ESDV). In addition, it helps to increase confident level and Safety Integration Level (SIL) of critical valves. Partial stroke test can be conducted manual by trained personnel and the testing can also be automated (PLC based) to minimize human error.
Nevertheless, there are some disadvantages of partial stroke test. Frequent testing of these valves promotes wear and tear and increases potential leakage and failure.
Following are some articles related to Partial Stroke Testing and you are encourages to read to enhance further your understanding.
On the hand, valves continuous move from one position to another position (e.g. full close to full open and vice versa) will minimize the chances of dirt and corrosion debris accumulation and get harden. A continuous moving valve with constant monitoring of it stroking time will enable alert of a out perform valve.
Partial stroke test is one of the testing procedures to ensure reliability and availability of valves. Normally the test is required for critical valve such as battery limit Emergency Shutdown Valves (ESDV). In addition, it helps to increase confident level and Safety Integration Level (SIL) of critical valves. Partial stroke test can be conducted manual by trained personnel and the testing can also be automated (PLC based) to minimize human error.
Nevertheless, there are some disadvantages of partial stroke test. Frequent testing of these valves promotes wear and tear and increases potential leakage and failure.
Following are some articles related to Partial Stroke Testing and you are encourages to read to enhance further your understanding.
- Need for an industry standard for ESD valves from engineering & safety point of view
- Partial Stroke Testing ESDV
- Partial Stroke Testing - Good & Bad and the Ugly
- The Partial Stroke Test as a module in the process safety concept
- Achieving High SIL Ratings with Partial Stroke Testing of Valves
- Should we install Butterfly valve for Pressure Relief Valve (PSV) isolation ?
- Another descrepancy found in API Std 521Jan 2007
- Controlled and Non-controlled Type Depressuring.
- How to apply valve equation in HYSYS Depressuring ?
- 12 Features required for Shutdown Valve (SDV)
- ERRATA - API Std 521, Pressure Relieving and Depressuring Systems
Labels: Emergency Shutdown, Safety
Wednesday, November 14, 2007
Today i have made more compilation for my previous posts.
If you have any suggestion or observation, please let me know.
POST per CATEGORY sort by ALPHABET D
POST per CATEGORY sort by ALPHABET E
POST per CATEGORY sort by ALPHABET F
Previous compilation...
Labels: General
Tuesday, November 13, 2007
I am compiling and sorting a listing of previous posts for ease of retrieval of present and new subscriber......Hope new subscriber will not miss my old posting and benefits from them...
This activities also make my previous posts can be easily located by everyone...
This activities also make my previous posts can be easily located by everyone...
If you have any suggestion or observation, please let me know.
Labels: General
Monday, November 12, 2007
I would think it is not proper to provide butterfly valve downstream of Pressure relief valve.
i) Isolation : This valve will shut close during Pressure relief valve inspection & testing. Wear-n-tear on butterfly valve seat will generally caused the valve can not be properly tie shut-off. Leakage and back-flow from downstream facilities i.e. flare poses potential hazard to operator and maintenance crew.
ii) Full passage area : Butterfly valve with valve disk in the middle can not provides 100% full area for relief flow passage. Full bore ball valve is generally can provide full area for relief flow passage.
iii) Internal blockage : Butterfly valve disk may be disconnected from the valve body without awareness of operator. It potential create partial or total blockage of the relief flow path which shall be avoided.
iv) Additional pressure drop : Even though the butterfly valve is full opened, as it can not provides 100% full passage area, additional pressure drop is observed on the line. It will crucial for inlet line with low set pressure system.
v) Solid accumulation : If the process fluid contains particle or solid, there is potential particle & solid settle at the valve disc, slow accumulation may increase partial blockage of the relief path.
vi) High potential of valve damage : As the valve disc is located in the center, large relief flow is impacting the disc. This increase the potential of valve disc disconnect from the valve body. Compare to full bore ball valve, this possibility is close to nil.
Ball valve is commonly used for Pressure Relief Valve isolation.
What do you think ?
Further Reading :
ii) Full passage area : Butterfly valve with valve disk in the middle can not provides 100% full area for relief flow passage. Full bore ball valve is generally can provide full area for relief flow passage.
iii) Internal blockage : Butterfly valve disk may be disconnected from the valve body without awareness of operator. It potential create partial or total blockage of the relief flow path which shall be avoided.
iv) Additional pressure drop : Even though the butterfly valve is full opened, as it can not provides 100% full passage area, additional pressure drop is observed on the line. It will crucial for inlet line with low set pressure system.
v) Solid accumulation : If the process fluid contains particle or solid, there is potential particle & solid settle at the valve disc, slow accumulation may increase partial blockage of the relief path.
vi) High potential of valve damage : As the valve disc is located in the center, large relief flow is impacting the disc. This increase the potential of valve disc disconnect from the valve body. Compare to full bore ball valve, this possibility is close to nil.
Ball valve is commonly used for Pressure Relief Valve isolation.
What do you think ?
Further Reading :
- Another descrepancy found in API Std 521Jan 2007
- Controlled and Non-controlled Type Depressuring.
- How to apply valve equation in HYSYS Depressuring ?
- 12 Features required for Shutdown Valve (SDV)
- ERRATA - API Std 521, Pressure Relieving and Depressuring Systems
- Requirement of overpressure protection devices on system design to PIPING code
Labels: Overpressure Protection, Pressure Relief Device
Sunday, November 11, 2007
Johnson Matthey Catalyst (JMC) and Dialog have organized The 2nd Mercury Technical Seminar in Pattaya, Thailand after their success story in the 1st Mercury Technical Seminar, 2005. The seminar covers paper presentation on the first day and demonstration of catalyst loading and unloading processes on second day.
There are about 206 participants mainly from oil and gas field such as PTTEP, Chevron, Technip, ConocoPhilips, Petronas, etc have attended this event. Experts from JMC, Intertek, C-Chec, Peco, Chevron and Mercury Technology Services have presented few papers. The papers include :
- Overview of mercury in Oil & Gas and its development
- Mercury removal technologies overview
- Pre & Post treatment - Filtration
- Protecting Petrochemical Plant from Mercury
- Mercury Sampling & Testing
- New technology – Mercury removal in liquid hydrocarbon
- Research & Development – future technologies
There are number of interesting points that I managed to capture which I think is rather important and crucial.
The following table presented mercury level for several crude & refinery product :
Present of mercury has reduced the crude / condensate price. JMC has developed and marketed it mercury removal in liquid hydrocarbon unit. Removal of mercury in liquid will definitely benefit the crude and condensate exporter by increasing the unit price.
ii) Intertek has conducted research in sampling and testing. They found that, mercury potentially adsorbed on the sampling bottle (glass) which may not be removed by simple solution rinsing. It needs to be extracted. The quantity of mercury shall be the tested medium reading plus extracted reading. This implies that those past laboratory testing results are under estimated the actual mercury content and shall be UPDATED.
iii) Second finding shown by Intertek is several samples collected at the same period from same sampling location showing different adsorption rate at the glass collection pot. This has created problem in bench marking mercury adsorbed on the glass pot. Intertek has used Teflon lined sampling pot which has more-less adsorbed mercury level.
iv) JMC has some break-through in mercury removal in aqueous system i.e. produced water and it is expected to be launched in the market next year. This no doubt is an great news to main oil and gas producer as there are having difficulties in disposing the produced and condensed water which contaminated with mercury.
The second day was the demonstration of catalyst loading and unloading process. See below image for the entire system.
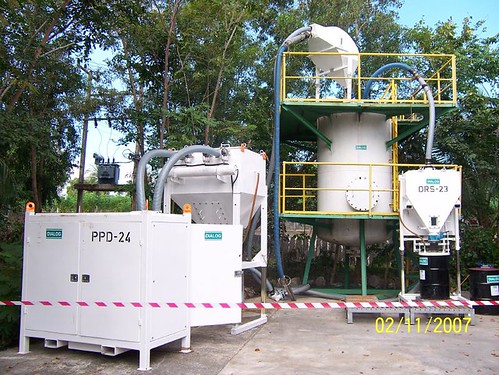
The following video clip shows catalyst LOADING process. (Click to view)
The following video clip shows catalyst UNLOADING process. (Click to view)
Further Reading :
i) In the past, there are a lot of success story in removal of mercury in Gas phase. Examples are Mercury removal unit (MRU) in Bongkot North, Pailin, Arthit field, etc. However, mercury removal in condensate (liquid hydrocarbon) and produced water are still yet to be developed. Generally the mercury will be send together with condensate and crude to onshore refinery for further treatment. This has reduced the crude / condensate price.
The following table presented mercury level for several crude & refinery product :
Present of mercury has reduced the crude / condensate price. JMC has developed and marketed it mercury removal in liquid hydrocarbon unit. Removal of mercury in liquid will definitely benefit the crude and condensate exporter by increasing the unit price.
ii) Intertek has conducted research in sampling and testing. They found that, mercury potentially adsorbed on the sampling bottle (glass) which may not be removed by simple solution rinsing. It needs to be extracted. The quantity of mercury shall be the tested medium reading plus extracted reading. This implies that those past laboratory testing results are under estimated the actual mercury content and shall be UPDATED.
iii) Second finding shown by Intertek is several samples collected at the same period from same sampling location showing different adsorption rate at the glass collection pot. This has created problem in bench marking mercury adsorbed on the glass pot. Intertek has used Teflon lined sampling pot which has more-less adsorbed mercury level.
iv) JMC has some break-through in mercury removal in aqueous system i.e. produced water and it is expected to be launched in the market next year. This no doubt is an great news to main oil and gas producer as there are having difficulties in disposing the produced and condensed water which contaminated with mercury.
The second day was the demonstration of catalyst loading and unloading process. See below image for the entire system.
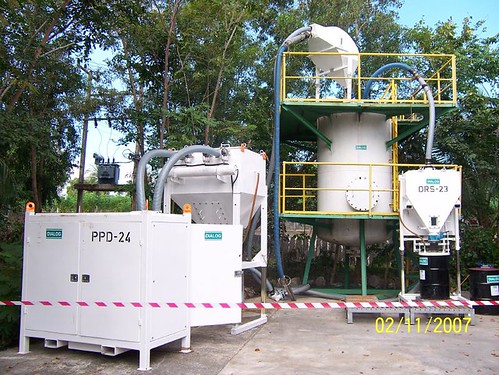
The following video clip shows catalyst LOADING process. (Click to view)
The following video clip shows catalyst UNLOADING process. (Click to view)
This seminar has provided me with market updates, new findings & technologies related to mercury removal, knowledge improvements, etc as well as some hands-on experience. You are encourage to participate in next Mercury Technical Seminar which probably will be held on 2009.
Labels: Mercury, Separation
Saturday, November 10, 2007
Recently i have made some search on the Gas Dynamic to further enhance my understanding on isothermal & adiabatic compressible flow, sonic velocity for ideal gas and real gas, etc. The main reason is to find the reason behind "Why k factor should NOT present in the Mach number calculation ?" which i have discussed in previous post. Mr. Leckner has provided some valuable inputs to me in one of the post that raised in CheResource forum. (Click HERE to read his responses). I just park the question there for sometime to get more inputs from other experts. Mean while i will make further study on gas dynamic...
In the process of searching information in internet, i found a very good site related to Compressible flow. This site is specifically dedicated to POTTO project.
What is POTTO project ?
The Potto Project was created Dr. Genick Bar-Meir and his friends to build FREE textbooks and software for college students. The Potto Project is under the open content license.
FUNDAMENTALS of COMPRESSIBLE FLOW
One of the FREE textbooks is FUNDAMENTALS of COMPRESSIBLE FLOW. Latest release is 0.4.8 which has been updated on Nov 05, 2007. You may download the FREE pdf file (Click HERE). You may also read online version. (Click HERE)
Part of the books :
Any interest to join his effort, please contact him (barmeir@gmail.com)
If you aware of other useful site, drop a note in comment column for benefit of all.
Further Reading :
In the process of searching information in internet, i found a very good site related to Compressible flow. This site is specifically dedicated to POTTO project.
What is POTTO project ?
The Potto Project was created Dr. Genick Bar-Meir and his friends to build FREE textbooks and software for college students. The Potto Project is under the open content license.
FUNDAMENTALS of COMPRESSIBLE FLOW
One of the FREE textbooks is FUNDAMENTALS of COMPRESSIBLE FLOW. Latest release is 0.4.8 which has been updated on Nov 05, 2007. You may download the FREE pdf file (Click HERE). You may also read online version. (Click HERE)
Part of the books :
- Introduction and history of this book
- History of Compressible Flow
- Speed of Sound
- Isentropic and isothermal Nozzle Flow
- Shock and moving shocks etc
- Gravity effects
- Isothermal Flow
- Fanno Flow
- Rayleigh Flow
- Filling and evacuating gaseous chambers
- Oblique Shock and Prandtl-Meyer Flow
- Program Explanation
- The Book subject and authors indexes
Any interest to join his effort, please contact him (barmeir@gmail.com)
If you aware of other useful site, drop a note in comment column for benefit of all.
Further Reading :
- Another descrepancy found in API Std 521 Jan 2007
- Controlled and Non-controlled Type Depressuring.
- How to apply valve equation in HYSYS Depressuring ?
- 12 Features required for Shutdown Valve (SDV)
- ERRATA - API Std 521, Pressure Relieving and Depressuring Systems
- Requirement of overpressure protection devices on system design to PIPING code
Labels: Ebook, Fluid Flow
Wednesday, November 7, 2007
In previous post, i have informed the first errata in API Std 521, edition Jan 2007. As expected more reading on this code found another discrepancy compare to previous version. This discrepancy is mainly due to REMOVAL of specific heat ratio (k) in the Mach number and Critical pressure calculation.
Equation [23] & [24] and [25] & [26] in API RP 521, 1997 (previous revision) are used to calculate the Mach number and Critical pressure of gas in the pipe.
Mach number
In imperial unit,
In metric unit,
Critical pressure
In imperial unit,
In metric unit,
After the API RP 521 is updated, similar equations used to calculate Mach number and Critical pressure has minimum modification.
Mach number
In imperial unit,
In metric unit,
Critical pressure
In imperial unit,
In metric unit,
Detail review on above equations, the specific heat capacity ratio (k) has been removed from the original equation. Is this a correction or an error ?
I have made some literature surveys and conduct some derivation works. Two main findings :
Based on simple derivation works, it ended-up with inclusion of k factor in the equation.
This discrepancy has been highlighted to API committee manager attention and quick response indicated equations in current edition (2007) are correct where k factor should not appear in those equations. Due to manning issue, no detail basis disclosed. Details searching do not find any supporting documents.
k factor generally range from 1.09 to 1.41 for most gases. Inverse square-root of k would range from0.84 to 0.96. Inclusion of k in the equation would probably bring down Mach number and critical pressure. Both impacts are partially balancing each and minimum impact to flowrate.
After further discussion and anaylsis, it's found that considering isothermal flow, the k factor should be omitted from the Mach number and critical pressure calculation. Details derivation may refer to "Removal of Specific Heat ratio (k) in the Mach No. & Critical Pressure Calculation".
Updated
- Nov 8, 2007 : This issue is being discussed in CheResource forum (Click HERE to view)
- Sept 28, 2008 : Post updated with omission of k factor.
- API R 521 1993 – No specific heat capacity ratio (k) included in the equation. However, API has included the k factor into the equation when it revised to API RP 1997. Once again, when it revised recently to 2007, the k factor has been removed again.
- Quick derivation showed that k factor should appear in the equation.
Based on simple derivation works, it ended-up with inclusion of k factor in the equation.
This discrepancy has been highlighted to API committee manager attention and quick response indicated equations in current edition (2007) are correct where k factor should not appear in those equations. Due to manning issue, no detail basis disclosed. Details searching do not find any supporting documents.
k factor generally range from 1.09 to 1.41 for most gases. Inverse square-root of k would range from0.84 to 0.96. Inclusion of k in the equation would probably bring down Mach number and critical pressure. Both impacts are partially balancing each and minimum impact to flowrate.
After further discussion and anaylsis, it's found that considering isothermal flow, the k factor should be omitted from the Mach number and critical pressure calculation. Details derivation may refer to "Removal of Specific Heat ratio (k) in the Mach No. & Critical Pressure Calculation".
Updated
- Nov 8, 2007 : This issue is being discussed in CheResource forum (Click HERE to view)
- Sept 28, 2008 : Post updated with omission of k factor.
Further Reading :
- Removal of Specific Heat ratio (k) in the Mach No. & Critical Pressure Calculation
- Controlled and Non-controlled Type Depressuring.
- How to apply valve equation in HYSYS Depressuring ?
- 12 Features required for Shutdown Valve (SDV)
- ERRATA - API Std 521, Pressure Relieving and Depressuring Systems
- Requirement of overpressure protection devices on system design to PIPING code
Labels: Depressurization, Loss Prevention, Overpressure Protection, Pressure Relief Device, Safety