Wednesday, August 20, 2008
Display problem ? Click HERE
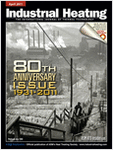
As the price of electricity, natural gas and other fossil fuels continues to climb, chemical processors are more closely examining high-temperature operations and heat-transfer systems to see if more efficiency can be had. In many cases
it can, and, as a result, heat-transfer projects are not only justifiable, but downright attractive.
There was a dialog among a few heat exchanger specialist from Alfa Laval, Paul Muller, Exergy LLC, etc. The dialog mainly discussed on strategy to improve heat transfer efficiency, heat recovery and efficient process control during this high energy price arena.
A few tips have been present :
- The energy crisis results high prices all of the time shorten paybacks. Energy efficient is one of the way to minimize cost
- Energy efficient heat transfer equipment such as Plate Heat exchanger, Gasketed Heat exchanger, Bonded Heat exchanger, etc is one of the option.
- For a service using Shell & Tube (S&T), the overall heat transfer coefficient (HTC) is around 300 Btu/h ft2°F. However, the overall heat transfer coefficient (HTC) for a compact heat exchanger can be improved 3-4 times (~1000 to 12000 Btu/h ft2°F).
- With lower overall heat transfer coefficient, this may translate into less space, smaller installation and handling cost. Capital cost may not be low as the fabrication cost for compact heat exchanger is high.
- Gasketed Heat exchanger good for maintenance. However shall take additional attention on the compatibility between gasket and fluid.
- All welded or Bonded heat exchanger may be considered if there is gasket & fluid compatible problem
- For laminar flow, heat transfer rate is only the function of fluid thermal conductivity. Operate heat transfer equipment at lamina flow during turndown could significantly reduce it heat transfer rate
- Compact heat exchanger promote turbulence. High turbulence increase heat transfer rate and reduce fouling (read more)
- Thus plant releasing hot exhaust gas from burner, boiler, gas turbine, etc to atmosphere may take the opportunity to recover heat
- Improve temperature control in process system would reduce energy usage
Not a CE subscriber... click here to subscribe FREE Chemical Engineering (CE)
Related Topic
- Practical Design Tips for Heat Exchanger Design
- COMPACT Heat Exchanger Increased Performance, Optimised area utilization, reduce CAPEX & OPEX
- Unexpected high cost of heat exchanger fouling...
- CFD in Compact Heat Exchanger
- Heat Transfer - Internal and External Flow
- Why Lower Fouling in Plate Heat Exchanger ?
Labels: Compact heat Exchanger, Heat Exchanger, Heat Recovery, Heat Transfer, Plate Heat Exchanger
0 Comments:
Post a Comment
Let us know your opinion !!! You can use some HTML tags, such as <b>, <i>, <a>
Subscribe to Post Comments [Atom]
Home:
<< Home