Thursday, July 31, 2008
Display problem ? Click HERE
Recommended :
- Subscribe FREE - Processing Magazine
- Tips on Succession in FREE Subscription
A catalytic-distillation process for the production of t-amyl-methyl-ether (TAME) from methanol and isoamylenes was simulated by developing the process model as a combination of unit operations from HYSYS operations palette. Geometrical characteristics of catalytic-distillation column are those of an industrial pilot plant and the results of simulation were compared with experimental data. The experimentally determined reactions kinetics was applied in the model. UNIQUAC-UNIFAC model equations were selected for the vapour-liquid equilibrium.
- Subscribe FREE - Processing Magazine
- Tips on Succession in FREE Subscription
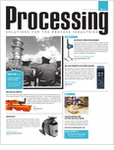
Catalytic Distillation Process Simulation using HYSYS
This paper presents a theoretical study for the modelling of reactive distillation column operation in t-amyl-methyl-ether (TAME) synthesis. The simulation procedure is based on a mathematical model considering chemical reaction kinetics for the main reactions and the vapour-liquid equilibrium. Phase contact in the reaction zone is described with the back-flow cell model.
The problem statement in HYSYS.Process environment was made considering three zones for the catalytic distillation column (rectifying, reaction and stripping). Constructive and operational characteristics of the column are specified as a consequence of the parametric study: reaction zone position, feed position and reflux ratio, in order to obtain maximum yield for the transformation of C5 reactive olefins in the pilot plant. The simulation results are in good agreement with experimental data obtained in the experimental pilot plant at SNP PETROM, INCERP Ploiesti subsidiary. The quality of the results obtained in this paper is limited by the uncertainty introduced by the phase hydrodynamics in the reaction zone the phase equilibrium hypothesis.
Read more here...
Related Topic
Read more here...
Related Topic
Labels: HYSYS, Process simulation
0 Comments:
Post a Comment
Let us know your opinion !!! You can use some HTML tags, such as <b>, <i>, <a>
Subscribe to Post Comments [Atom]
Home:
<< Home