Friday, July 25, 2008
Display problem ? Click HERE
CLICK HERE to Subscibe FREE...
Chemical Engineering (CE) released a special issue for Flowmeter & Piping recently. There are available FREE for subscribers. If you are not a CE subscriber yet, you may subscribes FREE issue of CE*** by clicking this link.
***The CE subscription is hot and may temporary unavailable. If it is unavailable, you are encouraged to revisit the link one week after. FREE CE subscription only for qualified professional.
Managing Measurement Costs in Automated Water Treatment Systems Using Smart Sensing and Blind Transmitter Technology
By Dave Vollaire, GF Piping Systems
Installed cost per measurement is an important factor for industrial water and wastewater treatment professionals focused on system design. Modern treatment systems are highly automated and a significant portion of equipment and installation cost belongs to measurement and instrumentation components. When installation costs are removed from the equation, it becomes clear that measurement and instrumentation components alone can account for up to 50 percent of the total equipment cost. Newer technologies such as smart sensing, multi-channel, multi-parameter instrumentation, as well as blind transmitter technology, can significantly reduce the cost per measurement over the traditional single point controller schemes in automated water treatment systems....
For CE subscriber only...Click here to read
(Not CE subscriber ? Try subscribes for FREE CE... Click HERE***)***The CE subscription is hot and may temporary unavailable. If it is unavailable, you are encouraged to revisit the link one week after. FREE CE subscription only for qualified professional.
Managing Measurement Costs in Automated Water Treatment Systems Using Smart Sensing and Blind Transmitter Technology
By Dave Vollaire, GF Piping Systems
Installed cost per measurement is an important factor for industrial water and wastewater treatment professionals focused on system design. Modern treatment systems are highly automated and a significant portion of equipment and installation cost belongs to measurement and instrumentation components. When installation costs are removed from the equation, it becomes clear that measurement and instrumentation components alone can account for up to 50 percent of the total equipment cost. Newer technologies such as smart sensing, multi-channel, multi-parameter instrumentation, as well as blind transmitter technology, can significantly reduce the cost per measurement over the traditional single point controller schemes in automated water treatment systems....
For CE subscriber only...Click here to read
GF Piping Systems New Metal Magmeter Configuration Expands Application Range and Versatility
By GF Piping Systems
TUSTIN, Calif. – June 26, 2008 – GF Piping Systems has added to its proven Signet 2552 Metal Magmeter family with the new Model 2552-3. The Signet Metal...
For CE subscriber only...Click here to read
(Not CE subscriber ? Try subscribes for FREE CE... Click HERE***)
For CE subscriber only...Click here to read
(Not CE subscriber ? Try subscribes for FREE CE... Click HERE***)
GF Piping Systems Introduces Next Generation DryLoc® pH and ORP Sensors Offering Enhanced Chemical Compatibility and Versatile Mounting Options
By GF Piping Systems
TUSTIN, Calif. – July 8, 2008 – GF Piping Systems has introduced the next generation of Signet DryLoc pH/ORP Sensors, Models 2724 − 2726. These sensors feature...
For CE subscriber only...Click here to read
(Not CE subscriber ? Try subscribes for FREE CE... Click HERE***)
For CE subscriber only...Click here to read
(Not CE subscriber ? Try subscribes for FREE CE... Click HERE***)
GF Piping Systems Introduces USB Interface for Signet Sensors, Offering Diagnostics, Parameter Configuration and Data Monitoring Capabilities
By GF Piping Systems
TUSTIN, Calif. – Nov. 8, 2007 – GF Piping Systems has introduced the Signet 3-0250, a new interface device that allows USB connection of blind Signet Sensors to...
For CE subscriber only...Click here to read
(Not CE subscriber ? Try subscribes for FREE CE... Click HERE***)
For CE subscriber only...Click here to read
(Not CE subscriber ? Try subscribes for FREE CE... Click HERE***)
FAYF - FLOWMETER SELECTION
by Rebekkah Marshall
Briefly discusses general selection criteria, flowmeter accuracy and turndown...
Click here...
Recommended :
Subscribe FREE - Processing Magazine
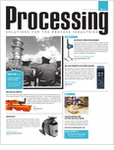
Piping for Process Plants Part 1: The Basics
Pipe, fittings and related equipment are fundamental to the operation of chemical process plants. The series of articles beginning with this one spells out the details. This is the first in a series of articles that will cover a wide range of piping topics. The topics will cross process-industry lines, pertaining to, for example, the chemical, petroleum-refining, pulp-and-paper and pharmaceutical and other industries.The main intent of these articles to address questions and misunderstandings as they relate to use of piping on a general basis.
Typical of the topics that will be covered in this series are the following:
* With respect to ASME flange ratings — Is the correct terminology 150- and 300-pound flange, or is it Class 150 and Class 300 flange? And do the 150 and 300 actually mean anything, or are they simply identifiers? Similarly, with respect to forged fittings, is the terminology 2,000-pound and 3,000-pound, or is it Class 2000 and Class 3000?
For CE subscriber only...Click here to download(Not CE subscriber ? Try subscribes for FREE CE... Click HERE***)
Piping Design, Part 2 - Flanges
The engineer or designer must choose among several flange options. Additional decisions involve facing and surface finishes, and the appropriate gaskets, bolts and nuts. Pipe flanges are used to mechanically connect pipe sections to other pipe sections, inline components, and equipment. Flanges also allow pipe to be assembled and disassembled without cutting or welding, which eliminates the need for those two operations when dismantling is required. In providing a breakable joint, however, flanges unfortunately provide a potential leak path for the process fluid contained in the pipe. Because of this, the usage of flanges needs to be minimized where possible, as with all other joints.
For CE subscriber only...Click here to download(Not CE subscriber ? Try subscribes for FREE CE... Click HERE***)
Piping Design, Part 3 - Design Elements
Design requires a systematic methodology, planning, technical ability, interdisciplinary coordination, foresight and, above all, experience. Piping design is the job of configuring the physical aspects of pipe and components in an effort to conform with piping and instrumentation diagrams (P&IDs), fluid-service requirements, associated material specifications, equipment-data sheets, and current good manufacturing practices (GMP) while meeting owner expectations. All of this must be accomplished within a pre-determined, three-dimensional assigned space, while coordinating the activity with that of the architecture, structural steel, HVAC (heating, ventilation air conditioning), electrical, video, data-and-security conduit and trays, and operational requirements.
For CE subscriber only...Click here to download(Not CE subscriber ? Try subscribes for FREE CE... Click HERE***)
Piping for Process Plants, Part 4: Codes and Fabrication
Besides flanges, there are also several different types of joints and welding processes to choose from. Additional decisions involve piping codes. This fourth in a series of articles* on piping for process plants examines two topics that may, at first, seem to fall outside the scope of chemical engineering — piping codes and the pipe fabrication. Obviously chemical engineers will not be welding pipes together, but understanding the benefits and limitations of different types of welding processes, for example, can help the engineer when designing the system that needs to be welded.
For CE subscriber only...Click here to download(Not CE subscriber ? Try subscribes for FREE CE... Click HERE***)
Piping Design Part 5: Installation and Cleaning
These practical guidelines for deciding which installation procedure to follow, and for cleaning a new pipeline system can prevent problems from happening during startup. This fifth in a series of articles [1 – 4] on piping design discusses the practical issues of installation and cleaning. The installation of pipe follows its fabrication and is very frequently a part of it. The installation of pipe can be accomplished in the following four primary ways, or combinations thereof:
For CE subscriber only...Click here to download(Not CE subscriber ? Try subscribes for FREE CE... Click HERE***)
Piping for Process Plants Part 6: Testing & Verification
Proper documentation, determination of the fluid service category and operating conditions are among the factors necessary to perform the correct leak test on a piping system. This sixth and final part of a series of articles [ 1 – 5] on piping for process plants discusses practical issues of leak testing and verification of piping systems. Leak testing and pressure testing are often used synonymously. However, pressure testing is a misnomer when referring to leak testing of piping systems. By definition, a pressure test is the procedure performed on a relief valve to test its set-point pressure. The intent, when pressure testing a relief valve, is not to check for leaks, but to test the pressure set point of the valve by gradually adding pressure to the relief valve until it lifts the valve off of the seat.
For CE subscriber only...Click here to download(Not CE subscriber ? Try subscribes for FREE CE... Click HERE***)
Related Post
- Flow Element (FE) Upstream or Downstream of Control Valve (CV) ?
- Use Ultra-Sonic Flowmeter in FLARE Gas Header for emission monitoring
- FAYF - Flowmeter selection in brief...
- Useful Documents Related to Control Valve
- Restrcition Orifice Used in Many Applications in Different Manners
- A refresh to Process Engineer on few phenomenons in restriction orifice
- Why Restriction Orifice is some distance from Blowdown valve ?
0 Comments:
Post a Comment
Let us know your opinion !!! You can use some HTML tags, such as <b>, <i>, <a>
Subscribe to Post Comments [Atom]
Home:
<< Home