Saturday, July 12, 2008
Recommended :
Subscribe FREE - Processing Magazine
A Pressure Relief Valve (PSV) is conventional type with bonnet vent to atmosphere. This PSV is protection a pressure vessel with pre-specified design pressure of 7 barg. Maximum expected operating pressure (MOP) of the system is about 6.2 barg. The vessel has a maximum allowable working pressure (MAWP) of 8 barg. The normal continuous superimposed back pressure (PBs) is zero barg (atmosphere). PSV set pressure (Pset) has been adjusted to be inline with design pressure (DP) of 7 barg. The PSV spring has been pre-set to open when the pressure is reach 7 barg. Disc area (Ad) and nozzle area (An) are 113mm2 and 71mm2 respectively (for illustration purpose only).
Subscribe FREE - Processing Magazine
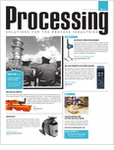
Now, plant debottlenecking has introduced a new Pressure control valve (PCV) continuous releasing vapor into the common flare header as the PSV. This has resulted a constant superimposed back pressure of 0.3 barg. As per early post "How Back Pressure Affect Conventional PSV Set Pressure Subject to It Vent", increases in superimposed back pressure will results the conventional PSV open prematurely (open at lower pressure), is the system still healthy ?
From above system description;
- PSV type : Conventional type PSV with bonnet vent to atmosphere.
- DP = 7 barg
- Pset (=Pv) = 7 barg
- MOP = 6.2 barg
- MAWP = 8 barg
- PBs,norm = zero barg (atmosphere)
- Ad = 113 mm2
- An = 71 mm2
The spring has been pre-set to open at DP = 7 barg and expected to reach complete opening at/below 7.7 barg.
After debottlenecking...
With superimposed back pressure, Pbs=0,
==> Fs = PvAn
After debottlenecking and new PCV results increased superimposed back pressure to P'b=Pbs=0.3 barg,
(P'v is new pressure causing PSV starts to open)
==> P'vAn = Fs - P'b(Ad-An)
==> P'vAn = PvAn - P'b(Ad-An)
==> P'v = Pv - P'b (Ad-An)/An
==> P'v = 7 - 0.3 (Ad-An)/An
==> P'v = 7 - 0.3 (113 -71)/71
==> P'v = 6.82 barg
Thus, PSV will open prematurely at P'v = 6.82 barg.
MOP / P'v = 6.2 / 6.82 = 90.2% marginally > 90%. This is still OK for conventional type PSV. In case the MOP / P'v is exceeded 90%, first shall check with PSV vendor if the PSV still acceptable. If the MOP / P'v is exceeded the acceptable range, a pilot operated PSV may be employed. It can accept normal MOP/Pset upto 95% (and 98% can be achieve for some manufacturer).
Built-up back pressure (Pbb) shall be calculated (say 0.4 barg),
Pbb / P'v = 0.4 / 6.82 = 5.8% < 10%. This is still OK for conventional type PSV.
After PSV set pressure is reset...
On the other hand, if operator would like to reset the PSV setting (F's) in order the PSV to open at 7 barg with superimposed back pressure of 0.3 barg, another assessment where the PCV is offline shall be checked. When PCV is offline, Pb = 0 barg.
After reseting, P'v = 7 barg, P'b = 0.3 barg,
==> P'vAn = F's - P'b(Ad-An)
==> F's = P'vAn + P'b(Ad-An)
When PCV is offline, superimposed back pressure will drop to P"b=0 barg,
with new opening pressure of P"v,
==> P"vAn = F's - P"b(Ad-An)
==> P"vAn = P'vAn + P'b(Ad-An) - P"b(Ad-An)
==> P"v = P'v + (P'b - P"b)(Ad-An)/An
==> P"v = 7 + (0.3-0)(113-71)/(71)
==> P"v = 7.18 barg
The new opening pressure will potentially 7.18 barg which is still below the Maximum Allowable Working pressure (MAWP) of 8 barg. Thus, this is still acceptable. In case the MAWP is lower than 7.18 barg, the new PSV setting shall be reduced accrodingly.
Observations
In this case study, there are some observation can be deduced :
- A conventional type PSV with bonnet vented to atmosphere, increases in superimposed back pressure will results conventional PSV open prematurely (open at lower pressure)
- Premature opening pressure shall be checked to maintain a healthy margin of 10% between Maximum operating pressure (MOP) and premature opening pressure
- New built-up back pressure shall be checked to ensure it still lower than 10% of premature opening pressure
- In case above healthy criteria can not be met, may consider reset the PSV spring setting in order to increase the set pressure of PSV
- With increase set pressure, the maximum opening pressure PSV shall be maintained below the Maximum allowable Working Pressure (MAWP) of protected system.
Related Post
- How Back Pressure Affect Conventional PSV Set Pressure Subject to It Vent
- Back Pressure Affect Conventional PSV Set Pressure : Case Study #2 - Non-Bonnect Vent
- Several Impact of Backpressure on Conventional PSV
- Simple Flow Chart to Determine Requirement of Thermal Relief
- Why Rupture (RD) Upstream of Pressure Relief Valve (PRV) ?
- Why Two Rupture Discs in Series ?
- Tube Rupture : Pressure Relief Valve (PSV) or Rupture Disk (RD) ?
- Criteria for Requirement of Pressure Relief Device for Tube Rupture
Labels: Overpressure Protection, Pressure Relief Device
0 Comments:
Post a Comment
Let us know your opinion !!! You can use some HTML tags, such as <b>, <i>, <a>
Subscribe to Post Comments [Atom]
Home:
<< Home