Monday, August 4, 2008
Display problem ? Click HERE
Recommended :
- Subscribe FREE - World Pumpv (USA & Europe only)
- Tips on Succession in FREE Subscription
There is a centrifugal pump working on the field and a flow meter is continuously measuring the flow rate delivered by the centrifugal pump. You noticed that flow meter indicating flow rate same as normal recorded flow rate, however, the downstream system indicating that there is reduction in flow. Flow meter Calibration is one of the normal way to confirm if the flow meter is working correctly. Prior to this, you may consider the following approach to quickly check if the pump delivering good flow and cross check with the flow meter.
This approach basically use the field tested pump curve as follow.
Pump power consumed by pump shaft,
Es = (dH x Q x SG) / (3960 x Pump Eff. x Kv) [Eq. 1]
where,
Es = Pump shaft power (HP) consumed
dH = Pump head (ft)
SG = fluid specific gravity
Pump Eff. = Pump efficiency
Kv = Viscosity Correction Factor
Power deliver by a motor to pump shaft,
Em = (1.732 x V x I x Motor Eff. x P.F.) / (746) [Eq. 2]
where,
Em = Power deliver by motor to pump shaft
V = Voltage (v)
I = Current (amp)
Motor eff. = Motor efficiency
P.F. = Motor Power Factor
Recommended :
- Subscribe FREE - Power Engineering (USA, Canada & Mexico)
- Subcribe FREE - Power Engineering (International)
Case study
A centrifugal pump transferring water from tank to a drum. A pressure transmitter located on the pump discharge. This estimated pump head based on differential pressure is 2000 ft. Fluid SG is 0.9932. From field, Voltage and current for the centrifugal pump are 460 volts and 323.1 amp. The flow meter is indicating flow rate of 385 gpm. Check if the flow meter is correctly measuring the flow rate.
From motor catalog, you may obtain motor efficiency (motor Eff.) and power factor (P.F.). For example, a motor with Motor Eff = 95% and P.F.=90%. The motor efficiency and P.F. may varies a bit (2%-5%). But they can be assumed same.
Power consumed / delivered,
From [Eq. 2],
==> Em = (1.732 x V x I x Motor Eff. x P.F.) / (746)
==> Em = (1.732 x 460 x 323.1 x 0.95 x 0.9) / (746)
==> Em = 295 HP
From above pump curve,
With Em = 295 HP
==> Flow, Q = 400 gpm, Pump Eff. 68% and Pump Head = 2000 ft.
Q = 400 gpm > 385 gpm as measured by flow meter. This indicates that the flow meter may not perform correctly.
Cross check with [Eq. 1],
As fluid is water,
==> Kv = 1.
For other type of fluid, may check out the viscosity correction factor using curve (by HI) presented in "Quick Check if Pump Performance Curve (Water) is Good for High Viscosity Fluid".
From [Eq. 1],
==> Es = (dH x Q x SG) / (3960 x Pump Eff. x Kv)
==> Q= Es x (3960 x Pump Eff. x Kv) / (dH x SG)
==> Q= 295 x (3960 x 0.68 x 1) / (2000 x 0.9932)
==> Q = 400 gpm
It is useful to generate a Current versus Flow curve as follow :
With this curve, operator may use it quickly check against the flow meter.
- Subscribe FREE - World Pumpv (USA & Europe only)
- Tips on Succession in FREE Subscription
This approach basically use the field tested pump curve as follow.
Pump power consumed by pump shaft,
Es = (dH x Q x SG) / (3960 x Pump Eff. x Kv) [Eq. 1]
where,
Es = Pump shaft power (HP) consumed
dH = Pump head (ft)
SG = fluid specific gravity
Pump Eff. = Pump efficiency
Kv = Viscosity Correction Factor
Power deliver by a motor to pump shaft,
Em = (1.732 x V x I x Motor Eff. x P.F.) / (746) [Eq. 2]
where,
Em = Power deliver by motor to pump shaft
V = Voltage (v)
I = Current (amp)
Motor eff. = Motor efficiency
P.F. = Motor Power Factor
Recommended :
- Subscribe FREE - Power Engineering (USA, Canada & Mexico)
- Subcribe FREE - Power Engineering (International)
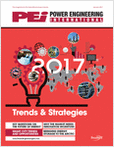
A centrifugal pump transferring water from tank to a drum. A pressure transmitter located on the pump discharge. This estimated pump head based on differential pressure is 2000 ft. Fluid SG is 0.9932. From field, Voltage and current for the centrifugal pump are 460 volts and 323.1 amp. The flow meter is indicating flow rate of 385 gpm. Check if the flow meter is correctly measuring the flow rate.
From motor catalog, you may obtain motor efficiency (motor Eff.) and power factor (P.F.). For example, a motor with Motor Eff = 95% and P.F.=90%. The motor efficiency and P.F. may varies a bit (2%-5%). But they can be assumed same.
Power consumed / delivered,
From [Eq. 2],
==> Em = (1.732 x V x I x Motor Eff. x P.F.) / (746)
==> Em = (1.732 x 460 x 323.1 x 0.95 x 0.9) / (746)
==> Em = 295 HP
From above pump curve,
With Em = 295 HP
==> Flow, Q = 400 gpm, Pump Eff. 68% and Pump Head = 2000 ft.
Q = 400 gpm > 385 gpm as measured by flow meter. This indicates that the flow meter may not perform correctly.
Cross check with [Eq. 1],
As fluid is water,
==> Kv = 1.
For other type of fluid, may check out the viscosity correction factor using curve (by HI) presented in "Quick Check if Pump Performance Curve (Water) is Good for High Viscosity Fluid".
From [Eq. 1],
==> Es = (dH x Q x SG) / (3960 x Pump Eff. x Kv)
==> Q= Es x (3960 x Pump Eff. x Kv) / (dH x SG)
==> Q= 295 x (3960 x 0.68 x 1) / (2000 x 0.9932)
==> Q = 400 gpm
It is useful to generate a Current versus Flow curve as follow :
Current versus Flow curve
With this curve, operator may use it quickly check against the flow meter.
Related Topic
- Is PumpSmart Right Solution for You ?
- Special Flowmeter & Piping Release...
- Vortex Breaker to Avoid Vapor Entrainment
- Estimate Minimum Submergence to Avoid Vapor Entrainment
- Estimate Pump Power Consumption without Vendor Information
- Trim Centrifugal Pump Impeller for Reduced Head
- Quick Check if Pump Performance Curve (Water) is Good for High Viscosity Fluid
2 Comments:
It is always better to choose a motor with 10 to 15 % higher so that motor amperage is below rated, this is for nmotor safety in case of variation of supply voltage and system P.F.
KLPai India
09449835098
The variation from calculation is about 2 %, this may be the error of mesuring instruments.Also the working oint and test point efficiancy of motr and pump itself will be differant.
KLPai India
094498 35098
Post a Comment
Let us know your opinion !!! You can use some HTML tags, such as <b>, <i>, <a>
Subscribe to Post Comments [Atom]
Home:
<< Home