Thursday, October 9, 2008
Display problem ? Click HERE
Recommended :
Subscribe FREE - Utility Automation & Engineering T&D
Carbon Dioxide (CO2), Hydrogen Sulphide (H2S), Mercury (Hg), Nitrogen (N2), Chloride (Cl) in formation water, etc are components present together in the feedstock for Oil and Gas production, refinery and Liquefied Natural Gas (LNG) production. Presence of CO2 and H2S with free water (H2O) can cause severe corrosion and Sulphide Stress Corrosion Cracking (SSCC) problems in
equipment and piping contact with the oil and gas. Read more in "What are the concerns related to H2S ?". Presence of Hg in Aluminum material i.e. coldbox and MCHE would lead to mercury embrittlement whilst Cl in hot stainless steel surface would lead to Chloride Stress Corrosion Cracking (CSCC). Read more in "Chloride Stress Corrosion Cracking & Use correct MOC for seawater service".
CO2 with presence of free water would lead to generation of Carbonic acid (H2CO3).
When Carbonic Acid contact with steel (Fe), reaction occur.
Useful Article Related to CO2 CorrosionSubscribe FREE - Utility Automation & Engineering T&D
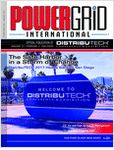
CO2 with presence of free water would lead to generation of Carbonic acid (H2CO3).
When Carbonic Acid contact with steel (Fe), reaction occur.
2Fe + H2CO3 ==> Fe2CO3 + H2
With minimum level of Oxygen would aggregate the corrosion :
Corrosion without Acid Carbonic :
and Corrosion with Acid Carbonic :
Carbonic acid is weak acid would reduce the pH of fluid and this further aggregate the corrosion.
Corrosion without Acid Carbonic :
and Corrosion with Acid Carbonic :
Carbonic acid is weak acid would reduce the pH of fluid and this further aggregate the corrosion.
Since the initial studies by DeWaard and Milliams'(1975), there are many other follow-up studies on the corrosion phenomena. Videm & Dugstad (1989), Dunlop, Hassell & Rhodes (1983), DeWaard, Lotz & Milliams (1991), But Dugstad (1992), DeWaard & Lotz (1993), Efird, Wright, Boros & Hailey (1993), Dugstad, Lunde & Videm (1994), etc have further studies the CO2 corrosion phenomenon. Following is compilation of articles related to CO2 Corrosion :
Integrated CO2 Corrosion - Multiphase Flow Model
An integrated CO2 corrosion – multiphase flow model was built which takes into account the effect of most important variables. The model is mechanistic in nature and resides on clear theoretical foundations. All the assumptions in the model are explicitly stated and are open to future adjustments and improvements. The overall model was extensively verified with a large experimental database and was able to perform reasonably well in all cases. The multiphase flow model was also benchmarked against a well-established commercial package.
CO2 Corrosion Mechanistic Modeling and Prediction in Horizontal Slug Flow
This paper presents a CO2 corrosion mechanistic model specifically developed for the horizontal multiphase slug flow. It covers electrochemical reactions at the steel surface, transport of reactive species between the metal surface and the bulk, and the chemistry in the bulk solution. The special mass transfer correlations in slug flow were applied in this model. The model can predict the corrosion rate in horizontal slug flow. Comparison with laboratory experimental corrosion results revealed that it could help the understanding of the internal corrosion of horizontal pipeline under slug flow condition. Furthermore, this model shows that the Froude number and the slug frequency are two important factors influencing the internal corrosion rates under multiphase slug flow. This provides an insight for the pipeline design and production under multiphase slug flow.
The Effect of CI- and Acetic Acid on Localized CO2 Corrosion in Wet Gas Flow
Wet gas corrosion rates of C1018 and X65 steel have been measured at the top and bottom of a
high pressure, 10 cm diameter horizontal pipeline under stratified flow conditions with different chloride (Cl-) concentrations. Experiments were performed for 200 hours at 90°C, CO2 partial pressure of 3.8 bar using a superficial gas velocity (Vsg) of 10 m/s and a superficial liquid velocity (Vsl) of 0.1 m/s. Three measurement techniques; ER, LPR, and WL were used simultaneously in the experiments. Localized corrosion occurred at the bottom of the pipe around the iron saturation point. The top of line was well protected by a thin corrosion product film and no localized corrosion was detected. C1018 and X65 have different sensitivities to pitting with a variation in Cl- concentration. Thus the pitting density concept is proposed to describe localized corrosion behavior. Surface analysis on iron carbonate films, by SEM and XRD, revealed different film thicknesses and crystal structures from the top to the bottom of the pipe. Cross-sectional analysis indicates that the thin corrosion product film, usually less than 10 microns, attached to the metal surface, is responsible for the low corrosion rate on top of the line, while the thick and porous film formed on the bottom, generally detached from the metal surface, was responsible for the initiation of localized corrosion.
Subscribes to FREE Hydrocarbon Processing
Top of Line Corrosion in Presence of Acetic Acid and Carbon Dioxide (CO2)
This paper deals with the phenomena of corrosion by acetic acid and carbon dioxide at the top of a horizontal pipeline under dewing conditions. The effect of different parameters known to influence the Top of the Line Corrosion (TLC), such as the condensation rate and the bulk temperature is studied. The free acetic acid concentration varies from 0 to 1000 ppm, the bulk temperature, is set mainly at 70oC, the condensation rate is varied while the partial pressure of carbon dioxide and the gas velocity are set at a fixed value. The presence of acetic acid increases the corrosion rate both at the top and at the bottom of the line in different ways. The condensation rate influences strongly the top of the line corrosion when it has a small influence at the bottom. Evidences of localized corrosion are found at the bottom of the line. The corrosion at the top is uniform in the experiments conducted.
CO2 Corrosion in the Presence of Trace Amounts of H2S
Experiments were conducted to determine the effect of an incremental change in the solution pH, from 4 to 6.6, on CO2 corrosion rates of AISI 1018 steel in the presence of H2S in both single phase flow (Vsl = 1 m/s) and multiphase flow (Vsg=3 m/s, Vsl= 1 m/s) in a large scale multiphase flow loop. Linear polarization probes, electrical resistance probes, and weight loss coupons were used to monitor corrosion rates during 4 to 10 day exposures to a CO2 saturated solution with trace amounts of H2S. The media for experimentation was a 1% NaCl solution at 60ºC, at 7.9 bar (100 psig) total pressure, with gas phase additions of H2S up to 100 ppm. Protective adherent films, seen under these conditions, limited corrosion rates in both single phase and multiphase flow conditions.
Iron carbonate scale growth and the effect of inhibition in CO2 corrosion of mild steel
Investigations were conducted to investigate iron carbonate scale precipitation, the interaction between a corrosion inhibition and the precipitating iron carbonate scale, and their effects on the corrosion rate. Both the effects of iron carbonate precipitation on inhibited and uninhibited surfaces and the effects of inhibition on surfaces with iron carbonate scale were studied. The experiments were done in glass cells at 80 °C and a iron carbonate supersaturation range of 7 – 150. A generic imidazoline based inhibitor was added at various points in the iron carbonate scale formation process. Both corrosion rates and precipitation rates were measured using electrochemical and weight gain/loss methods. The scale was later analyzed using scanning electron microscopy (SEM). It was found that the dissolved ferrous ion concentration method, used previously, overestimates the rate of iron carbonate precipitation. Although no antagonism was found under any of other conditions tested, it was seen that the addition of the inhibitor retarded the growth of the iron carbonate scale.
Effect of acetic acid, pH and MEG on the CO2 top of the line corrosion
This research work presents a study of Top of the Line Corrosion (TLC) on carbon steels in the
presence of carbon dioxide and acetic acid. The influence of different parameters such as the presence of mono-ethylene glycol (MEG) and the use of pH control were studied in a 4” diameter flow loop. Two sets of experiments were conducted; one at 70ºC, high CO2 partial pressure and a “critical” condensation rate and another one at 80ºC, low CO2 partial pressure and a high condensation rate. Weight loss techniques and surface analysis were used to evaluate the corrosion rate and products. It was found that the presence of HAc at the concentrations evaluated does not affect the general corrosion rate at the top of the line. Top of the line corrosion rates correlate with the De Waard / Lotz estimate of 10% of bottom of the line rates15. It is believed that the corrosion mechanism is still controlled by CO2 partial pressure at the experimental conditions evaluated in this study. The presence of MEG has not shown any effect on TLC due to the fact that the condensation rate was kept constant. The use of pH control in the supply is believed to limit the amount of HAc in the condensed water. No clear evidence of localized corrosion or pits can be reported at this stage of the study due to the short time of exposure.
CO2/H2S corrosion under scale forming conditions
Three different mild steel coupons with two different surface areas were exposed to a CO2 saturated multiphase environment with a trace amount of hydrogen sulfide under supersaturated scale forming conditions designed to increase the probability of localized corrosion. Corrosion testing was conducted in the region of low supersaturation values for iron carbonate (SSFeCO3 < 10) and three different supersaturation values for iron sulfide (2.5 < SSFeS < 125) through adjustment of the partial pressure of H2S during 30 day exposures to system conditions. Experiments were conducted in a 1% NaCl solution at 60ºC, pH 6.0, 0.77MPa partial pressure CO2 with trace amounts of H2S in both single phase flow (Vsl = 1 m/s) and multiphase flow (Vsg=3 m/s, Vsl= 1 m/s). Under the conditions tested, both siderite and mackinawite films were developed as adherent corrosion product films. Localized corrosion was observed.
Click CO2 Corrosion in Oil & Gas - Part 2 to continue...
Related Post
Integrated CO2 Corrosion - Multiphase Flow Model
An integrated CO2 corrosion – multiphase flow model was built which takes into account the effect of most important variables. The model is mechanistic in nature and resides on clear theoretical foundations. All the assumptions in the model are explicitly stated and are open to future adjustments and improvements. The overall model was extensively verified with a large experimental database and was able to perform reasonably well in all cases. The multiphase flow model was also benchmarked against a well-established commercial package.
CO2 Corrosion Mechanistic Modeling and Prediction in Horizontal Slug Flow
This paper presents a CO2 corrosion mechanistic model specifically developed for the horizontal multiphase slug flow. It covers electrochemical reactions at the steel surface, transport of reactive species between the metal surface and the bulk, and the chemistry in the bulk solution. The special mass transfer correlations in slug flow were applied in this model. The model can predict the corrosion rate in horizontal slug flow. Comparison with laboratory experimental corrosion results revealed that it could help the understanding of the internal corrosion of horizontal pipeline under slug flow condition. Furthermore, this model shows that the Froude number and the slug frequency are two important factors influencing the internal corrosion rates under multiphase slug flow. This provides an insight for the pipeline design and production under multiphase slug flow.
The Effect of CI- and Acetic Acid on Localized CO2 Corrosion in Wet Gas Flow
Wet gas corrosion rates of C1018 and X65 steel have been measured at the top and bottom of a
high pressure, 10 cm diameter horizontal pipeline under stratified flow conditions with different chloride (Cl-) concentrations. Experiments were performed for 200 hours at 90°C, CO2 partial pressure of 3.8 bar using a superficial gas velocity (Vsg) of 10 m/s and a superficial liquid velocity (Vsl) of 0.1 m/s. Three measurement techniques; ER, LPR, and WL were used simultaneously in the experiments. Localized corrosion occurred at the bottom of the pipe around the iron saturation point. The top of line was well protected by a thin corrosion product film and no localized corrosion was detected. C1018 and X65 have different sensitivities to pitting with a variation in Cl- concentration. Thus the pitting density concept is proposed to describe localized corrosion behavior. Surface analysis on iron carbonate films, by SEM and XRD, revealed different film thicknesses and crystal structures from the top to the bottom of the pipe. Cross-sectional analysis indicates that the thin corrosion product film, usually less than 10 microns, attached to the metal surface, is responsible for the low corrosion rate on top of the line, while the thick and porous film formed on the bottom, generally detached from the metal surface, was responsible for the initiation of localized corrosion.
Subscribes to FREE Hydrocarbon Processing
This paper deals with the phenomena of corrosion by acetic acid and carbon dioxide at the top of a horizontal pipeline under dewing conditions. The effect of different parameters known to influence the Top of the Line Corrosion (TLC), such as the condensation rate and the bulk temperature is studied. The free acetic acid concentration varies from 0 to 1000 ppm, the bulk temperature, is set mainly at 70oC, the condensation rate is varied while the partial pressure of carbon dioxide and the gas velocity are set at a fixed value. The presence of acetic acid increases the corrosion rate both at the top and at the bottom of the line in different ways. The condensation rate influences strongly the top of the line corrosion when it has a small influence at the bottom. Evidences of localized corrosion are found at the bottom of the line. The corrosion at the top is uniform in the experiments conducted.
CO2 Corrosion in the Presence of Trace Amounts of H2S
Experiments were conducted to determine the effect of an incremental change in the solution pH, from 4 to 6.6, on CO2 corrosion rates of AISI 1018 steel in the presence of H2S in both single phase flow (Vsl = 1 m/s) and multiphase flow (Vsg=3 m/s, Vsl= 1 m/s) in a large scale multiphase flow loop. Linear polarization probes, electrical resistance probes, and weight loss coupons were used to monitor corrosion rates during 4 to 10 day exposures to a CO2 saturated solution with trace amounts of H2S. The media for experimentation was a 1% NaCl solution at 60ºC, at 7.9 bar (100 psig) total pressure, with gas phase additions of H2S up to 100 ppm. Protective adherent films, seen under these conditions, limited corrosion rates in both single phase and multiphase flow conditions.
Iron carbonate scale growth and the effect of inhibition in CO2 corrosion of mild steel
Investigations were conducted to investigate iron carbonate scale precipitation, the interaction between a corrosion inhibition and the precipitating iron carbonate scale, and their effects on the corrosion rate. Both the effects of iron carbonate precipitation on inhibited and uninhibited surfaces and the effects of inhibition on surfaces with iron carbonate scale were studied. The experiments were done in glass cells at 80 °C and a iron carbonate supersaturation range of 7 – 150. A generic imidazoline based inhibitor was added at various points in the iron carbonate scale formation process. Both corrosion rates and precipitation rates were measured using electrochemical and weight gain/loss methods. The scale was later analyzed using scanning electron microscopy (SEM). It was found that the dissolved ferrous ion concentration method, used previously, overestimates the rate of iron carbonate precipitation. Although no antagonism was found under any of other conditions tested, it was seen that the addition of the inhibitor retarded the growth of the iron carbonate scale.
Effect of acetic acid, pH and MEG on the CO2 top of the line corrosion
This research work presents a study of Top of the Line Corrosion (TLC) on carbon steels in the
presence of carbon dioxide and acetic acid. The influence of different parameters such as the presence of mono-ethylene glycol (MEG) and the use of pH control were studied in a 4” diameter flow loop. Two sets of experiments were conducted; one at 70ºC, high CO2 partial pressure and a “critical” condensation rate and another one at 80ºC, low CO2 partial pressure and a high condensation rate. Weight loss techniques and surface analysis were used to evaluate the corrosion rate and products. It was found that the presence of HAc at the concentrations evaluated does not affect the general corrosion rate at the top of the line. Top of the line corrosion rates correlate with the De Waard / Lotz estimate of 10% of bottom of the line rates15. It is believed that the corrosion mechanism is still controlled by CO2 partial pressure at the experimental conditions evaluated in this study. The presence of MEG has not shown any effect on TLC due to the fact that the condensation rate was kept constant. The use of pH control in the supply is believed to limit the amount of HAc in the condensed water. No clear evidence of localized corrosion or pits can be reported at this stage of the study due to the short time of exposure.
CO2/H2S corrosion under scale forming conditions
Three different mild steel coupons with two different surface areas were exposed to a CO2 saturated multiphase environment with a trace amount of hydrogen sulfide under supersaturated scale forming conditions designed to increase the probability of localized corrosion. Corrosion testing was conducted in the region of low supersaturation values for iron carbonate (SSFeCO3 < 10) and three different supersaturation values for iron sulfide (2.5 < SSFeS < 125) through adjustment of the partial pressure of H2S during 30 day exposures to system conditions. Experiments were conducted in a 1% NaCl solution at 60ºC, pH 6.0, 0.77MPa partial pressure CO2 with trace amounts of H2S in both single phase flow (Vsl = 1 m/s) and multiphase flow (Vsg=3 m/s, Vsl= 1 m/s). Under the conditions tested, both siderite and mackinawite films were developed as adherent corrosion product films. Localized corrosion was observed.
Click CO2 Corrosion in Oil & Gas - Part 2 to continue...
Related Post
- What are the concerns related to H2S ?
- Several Concerns in High CO2 Field Development
- How does Supercritical fluid looks like ?
- High Temperature Hydrogen Attack in metal & alloy
- Hydrogen Embrittlement TEST method
- Chlorride stress corrosion cracking and use of correct MOC for seawater
- Pitting Corrosion - Mechanism & Prevention
- How a Chloride Stress Corrosion Cracking Lookslike ?
Labels: Chloride Stress Corrosion Cracking, CO2, Corrosion
0 Comments:
Post a Comment
Let us know your opinion !!! You can use some HTML tags, such as <b>, <i>, <a>
Subscribe to Post Comments [Atom]
Home:
<< Home