Monday, September 22, 2008
Display problem ? Click HERE
A pressure containment equipment shall be pressure tested before it is authorized to be in real world service. Once the equipment is pressure tested, the equipment integrity is preserved. However, failure in testing the equipment would creates safety concerns to all level of personnel.
Recommended :Subscribe FREE - Processing Magazine
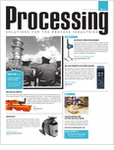
Testing Medium Selection
Pressure test is normally carried out using air (pneumatic test) and water (hydrostatic test). In some event for some equipment i.e reactor, inert gases (e.g., nitrogen) or liquids are used as air or water would possibly create concerns i.e. corrosion, cracking, etc to the equipment. Proper selection of testing medium is one of the critical task which shall involve process and chemical designer. Several aspect shall be checked for the selection of testing medium :
i) Corrosion cracking i.e. Chloride Stress Corrosion Cracking (CSCC) in stainless steel vessel due to present of Chloride in water
ii) Metal embrittlement i.e. Mercury embrittlement in aluminum heat exchanger due to present of mercury in air
iii) Present of low pocket in equipment will trap water if water or wet air is used. Water stay in the equipment promote corrosion
iv) Equipment handling vapor or gas, preferentially pressure test with air and vice versa
v) Selection of testing medium could also subject to the pre-commissioning activities. For example, large amount of water used for slugcatcher hydrostatic testing may be transferred to other equipment for hydrostatic testing or water circulation test.
vi) Mixture of air and water sometime is employed to save cost.
The great advantage of using air or water compare to other fluid are easy handling, cheap testing cost, less / no corrosion and cracking to many type of material.
Pressure Testing Failure
As many newly fabricated equipment subject to pressure test, equipment failure during pressure test may occur and could lead to catastrophe. Following are some failure incidents during process preparation and implementation of pressure test.
i) Vessel cracked during hydrostatic test.
ii) Overpressure during preparation of hydrostatic. Tank top blew off due to high water filling (using hydrant) rate with low capacity relief valve.
iii) Tank collapsed during emptying of water after hydrostatic test. Plastic coversheet block air inlet and create vacuum. Read more Vacuum
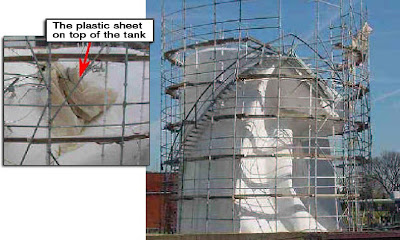
i) Corrosion cracking i.e. Chloride Stress Corrosion Cracking (CSCC) in stainless steel vessel due to present of Chloride in water
ii) Metal embrittlement i.e. Mercury embrittlement in aluminum heat exchanger due to present of mercury in air
iii) Present of low pocket in equipment will trap water if water or wet air is used. Water stay in the equipment promote corrosion
iv) Equipment handling vapor or gas, preferentially pressure test with air and vice versa
v) Selection of testing medium could also subject to the pre-commissioning activities. For example, large amount of water used for slugcatcher hydrostatic testing may be transferred to other equipment for hydrostatic testing or water circulation test.
vi) Mixture of air and water sometime is employed to save cost.
The great advantage of using air or water compare to other fluid are easy handling, cheap testing cost, less / no corrosion and cracking to many type of material.
Pressure Testing Failure
As many newly fabricated equipment subject to pressure test, equipment failure during pressure test may occur and could lead to catastrophe. Following are some failure incidents during process preparation and implementation of pressure test.
i) Vessel cracked during hydrostatic test.
ii) Overpressure during preparation of hydrostatic. Tank top blew off due to high water filling (using hydrant) rate with low capacity relief valve.
iii) Tank collapsed during emptying of water after hydrostatic test. Plastic coversheet block air inlet and create vacuum. Read more Vacuum
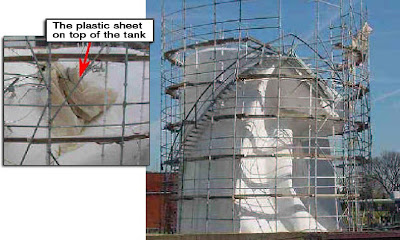
iv) Sphere tank collapse during water filling due to severe corrosion on the support.
* all images are courtesy of www.oilandgasconstruction.com
Some Guidelines
Thus, do not underestimate the safety issue during pressure testing. Any equipment could failed if improper handling is used. Several guidelines on pressure testing are listed :
Related Post
* all images are courtesy of www.oilandgasconstruction.com
Some Guidelines
Thus, do not underestimate the safety issue during pressure testing. Any equipment could failed if improper handling is used. Several guidelines on pressure testing are listed :
- Check testing medium compatibility
- Check water and /or air supply pressure is sufficient
- Ensure venting capacity is sufficient for filling rate
- Ensure the vent is large enough to avoid vacuum during water emptying after hydrostatic test if the tank or vessel is not designed to full vacuum
- Check vessel support and foundation is fit for liquid or water testing during preparation especially testing for used equipment. Corrosion is one of major concern
- Present of internal i.e. mist mesh, bubble cap, valve tray, etc could create restriction and potentially lead to partial vacuum. Drain water in control manner.
- Keep personnel away
Related Post
- Vacuum Hazard - Another Catastrophic Factor...
- 4-steps Approach to Combat Vacuum Hazard
- Dust Explosion Basic & Protection
- Blast rocks Texas oil refinery
- Design fault in Hydrogen Attack of Residue Hydrodesulfurrization
Labels: Overpressure Protection
0 Comments:
Post a Comment
Let us know your opinion !!! You can use some HTML tags, such as <b>, <i>, <a>
Subscribe to Post Comments [Atom]
Home:
<< Home