Saturday, February 7, 2009
Display problem ? Click HERE
Recommended :

Product fluid in reactor involve exothermic process is commonly hot. It is then sent to distillation and separation system for catalyst and raw material recovery. Separated product is then cooled by plant wide Cooling Water (CW) before it is sent to storage tank. The product temperature will have to be maintained.
How this temperature is controlled ?
Temperature Control Methods
There are several ways to maintain the product temperature :
(i) Provide a product bypass across the Cooler, control valves on Product bypass line and Outlet line (Split range control) with fixed CW flowrate
(ii) Provide a CW bypass across the Cooler, control valves on CW bypass line and CW inlet to Cooler with full product flow across cooler
(iii) Provide a CW bypass across the Cooler, control valves on CW bypass line and CW outlet to Cooler with full product flow across cooler
(iv) Provide a Control valve at the Cooler inlet with full product flow across cooler
(v) Provide a Control valve at the Cooler outlet with full product flow across cooler
Generally the product flow is fixed by operator based on production plan and the product flow shall not be controlled. Thus, it is always not recommended to provide a control valve at the inlet and outlet of product line for product temperature control.
Disturbance of CW Network Balance
Cooling water is in a network supplying to many heat exchanger through out the plant for cooling purpose. It is normally supplied by a set of centrifugal pump. As centrifugal pump head will be affected flow across, any changes in the CW demand will affect the CW balance in network. This will further affect the pressure in the network and hence the CW flow into other heat exchangers. Thus, it is always recommended not to throttle the CW flow as much as possible to avoid CW balance.
Scaling
Throttling CW flow into heat exchanger would potential lead to low CW flow into heat exchanger, high film temperature at on CW side and promote scaling. The option (ii) and (iii) are always recommended IF throttling on CW side is chosen.
Potential affecting Production
Controlling product fluid temperature with product bypass across the Cooler, control valves on Product bypass line and Outlet line (Split range control) and fixed CW flowrate (option i) is one of the common way in temperature control for product cooling. As it minimize the impact to CW network. Nevertheless, there is still concern about manipulating product fluid or mal-operation (controller failure) of control valves would potentially lead to production lost, the option (ii) and (iii) are always the recommended option.
CW Pressurise or Non-Pressurise
Option (ii) and (iv) compare to option (iii) and (v), the difference is the location of main CW line control valve (either at the inlet or the outlet). Providing a control valve at the outlet will have the following advantages :
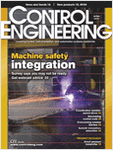
a) Maintain high pressure in the heat exchanger and higher pressure will results higher heat transfer
b) CW at high pressure will minimise potential of boiling
c) CW at high pressure will minimise potential release of dissolved gases in CW , trap in heat exchanger and reduce heat transfer
d) In event of Control valve failure (failed to full close position), not further Cooling. CW in the heat exchanger will be heated and potentially lead to heat exchanger overpresure due to thermal expansion and/or boiling. The CW will be relieved via Pressure Relief Device provided on the heat exchanger. Providing control valve at the outlet would allow continue CW feeding into the heat exchanger, this minimise the potential of sudden temperature increase and cause heat exchanger due to thermal shock. The downside is release CW into disposal network.
Considering above advantages, it is always recommended to provide control valve on CW line at the outlet IF throttling CW side is chooses.
CONTROLLING SHELL AND TUBE EXCHANGERS
"Controlling Shell & Tube Heat Exchanger", an excellent article by Walter Driedger discussed about all type of control schemes around heat exchanger. Check out.
Related Topic
- Problems and Measures for Condensate Recycle Control Valve
- FAQ Related to Control Valves
- Useful Documents Related to Control Valve
- FREE & Reliable Control Valve Sizing Software
- Anti-surge Control (ASC) or Capacity Control (CC) Valve in Vertical Upward Run ?
- Combine Anti-surge control (ASC) & Capacity Control (CC) Functions ?
Labels: Control valve, Heat Exchanger
0 Comments:
Post a Comment
Let us know your opinion !!! You can use some HTML tags, such as <b>, <i>, <a>
Subscribe to Post Comments [Atom]
Home:
<< Home